Wertstromanalyse & Wertstromdesign
Was ist eine Wertstromanalyse und was ist ein Wertstromdesign? Warum ist die Wertstromanalyse die Methode der Wahl in der Beratung? Warum ist Veränderung überhaupt notwendig? Wie läuft eine Wertstromanalyse genau ab? Was bedeutet „Go to Gemba“ und „Go & See“ und was ist ein „Sensei“?
All diese Fragen werden in diesem Beitrag beantwortet. Wir wünschen Ihnen viel Freunde und eine interessante Lernerfahrung beim Lesen dieses Beitrags!
Zusammenfassung
- Eine Wertstromanalyse ist das zentrale Werkzeug in der Lean Beratung.
- Eine Wertstromanalyse betrachtet einen oder mehrere Kernprozesse bzw. Kernwertströme mit denen die zentrale Wertschöpfung des Unternehmens erzeugt wird.
- In der Regel wird der gesamte Prozessfluss, Materialfluss und Informationsfluss vom Rohmaterial bis zum fertigen Produkt analysiert.
- Es wird ermittelt, wie lange es dauert, bis ein Produkt den Prozess bis zur Fertigstellung durchlaufen hat. Die Durchlaufzeit (DLZ) ist eine zentrale Kennzahl im Lean Management.
- Als Wertschöpfung werden alle Tätigkeiten am Produkt bezeichnet welche dessen Wert aus Kundensicht erhöhen. Verschwendung sind nach dieser Definition alle anderen Tätigkeiten wie z.B. Transport, Handling, ein- und auslagern, Rückfragen usw..
- Die im Prozess liegende Wertschöpfung wird von Verschwendung getrennt und die wesentlichen Probleme und Störungen im Prozess ermittelt.
- Da die Wertschöpfung den kleinsten Anteil der Durchlaufzeit bildet, fokussiert die Beratung vor allem auf die Reduzierung von Verschwendung und nicht primär auf die Optimierung von wertschöpfenden Anteilen im Prozess.
- Das Ziel der Wertstromanalyse ist es mit dem Wertstromdesign einen neuen, besseren Prozess zu entwickeln, dessen Durchlaufzeit reduziert ist.
- Auf der Basis dieses Wertstromdesigns werden Leanprojekte definiert, mit deren Hilfe der neue Wertstrom erreicht werden soll.
- Diese Lernprojekte werden im Rahmen einer Lean Transformation im Lean Masterplan nachverfolgt.

Warum ist Veränderung notwendig? Preise sinken – Kosten steigen!
Zu Beginn einer Wertstromanalyse steht immer die Frage, warum eine Veränderung überhaupt erfolgen sollte. Meist ist die Situation im Unternehmen noch einigermaßen zufriedenstellend. Es gibt zwar Warnsignale, aber die handelnden Personen sehen noch keinen echten Veränderungsdruck.
Dann ist es hilfreich noch einmal darzustellen, warum Veränderungen und explizit Projekte zur Kostenreduzierung ein elementarer Bestandteil in einem gesunden Unternehmen sein muss.
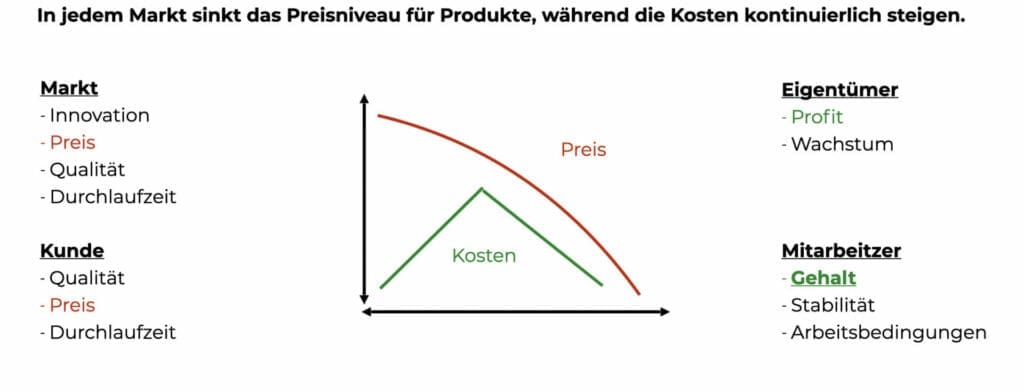
Während der Markt und Kunden stetig niedrigere Preise für ein innovatives Produkt zahlen wollen (bei bester Qualität und kurzer Durchlaufzeit), verlangen die Eigentümer und Mitarbeiter stetig höhere Profite und steigende Gehälter.
Jedes Unternehmen ist daher mit dem Konflikt zwischen steigenden Kosten und sinkenden Preisen konfrontiert. Daher ist jedes Unternehmen zu einem bestimmten Zeitpunkt dazu gezwungen die Kosten zu reduzieren und die Produktivität zu erhöhen.
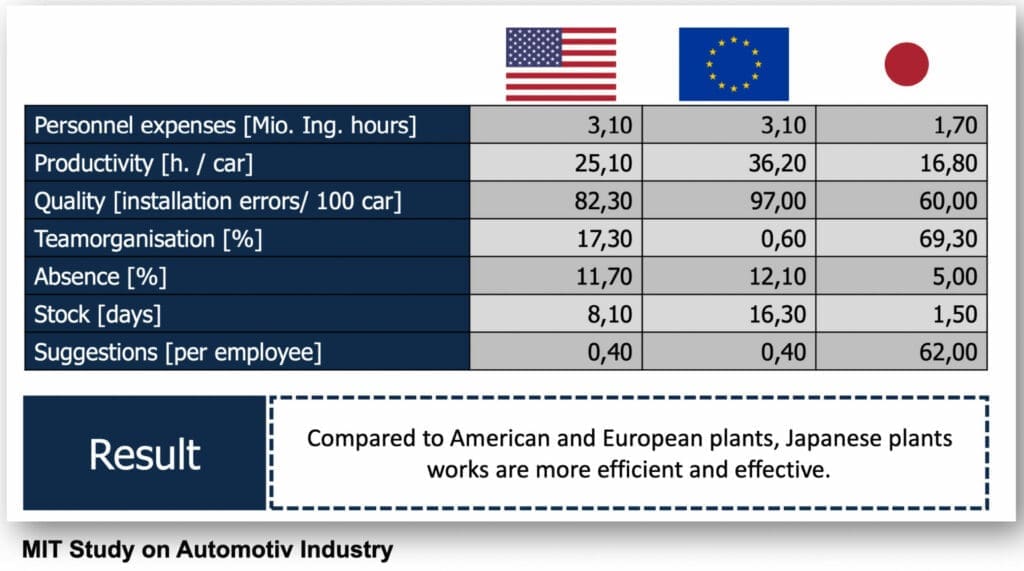
Diese Dynamik lässt sich gut am Beispiel der Automobilindustrie vergegenwärtigen. Diese ältere Studie vom Massachusetts Institut of Technology, USA zeigt die erheblichen Unterschiede in der Produktivität zwischen Amerikanischen, Europäischen und Japanischen Autoherstellern auf. Die Marktdynamik fordert von jedem Teilnehmer ständige Verbesserung der Herstellungsprozesse.
Go to Gemba – Gemba Genbutsu
Es gibt keinen lehrreicheren, ehrlichere Ort als die Gemba – den Shopfloor, also der Ort an dem die Arbeit stattfindet. Denn der Shopfloor erzählt immer die Wahrheit. Das Wesen eines Unternehmens zeigt sich in der Art und Weise, wie der Shopfloor organisiert ist.
Deshalb ist es so entscheidend Zeit auf dem Shopfloor zu verbringen. Wer den Shopfloor lesen kann, erkennt die Stärken und Herausforderungen eines Unternehmens.
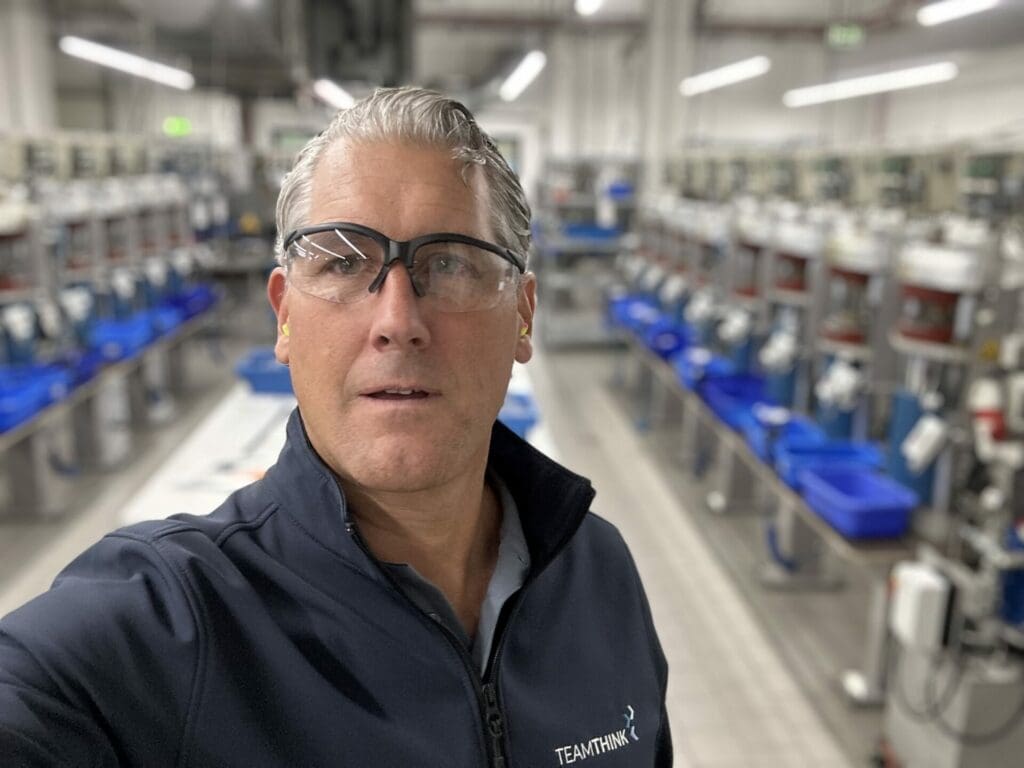
In der Lean Welt heißt es „Go to Gemba“ was sich aus dem japanischen Begriff „Gemba Genbutsu“ ableitet. Übersetzt bedeutet es wörtlich „realer Ort, reale Sache“ und ist ein Schlüsselprinzip des Toyota-Produktionssystems.
Das Prinzip wird auch als „Go & See“ oder „gehen und sehen“ bezeichnet. Gemeint ist, dass alle Managementprozesse das Ziel haben müssen, den Prozess der Wertschöpfung auf dem Shopfloor zu vereinfachen. Deshalb sind Manager im Toyota-Produktionssystem angehalten, auf den Shopfloor „gehen“ und zu „beachten“. wie der Prozess der Wertschöpfung verbessert werden kann.
Der Sensei
Ein Lean Sensei ist ein Experte für Lean Management, der Unternehmen bei der Umsetzung effizienterer Prozesse unterstützt. Der japanische Betritt „Sensei“ bedeutet übersetzt „Lehrer oder Lehrmeister“ und wird auch als Anrede verwandt.
Ein Sensei ist ein Lean Experte mit besonders viel Erfahrung und oder Branchen Know-How, der in der Lage ist, Kunden durch das schwierige Terrain von Lean Transformationsprojekten zu begleiten.
Ein Sensei betrachtet nicht nur die fachliche Themen der Transformation, sondern legt einen großen Schwerpunkt auf die Entwicklung der Führungsfähigkeiten der Führungskräfte.
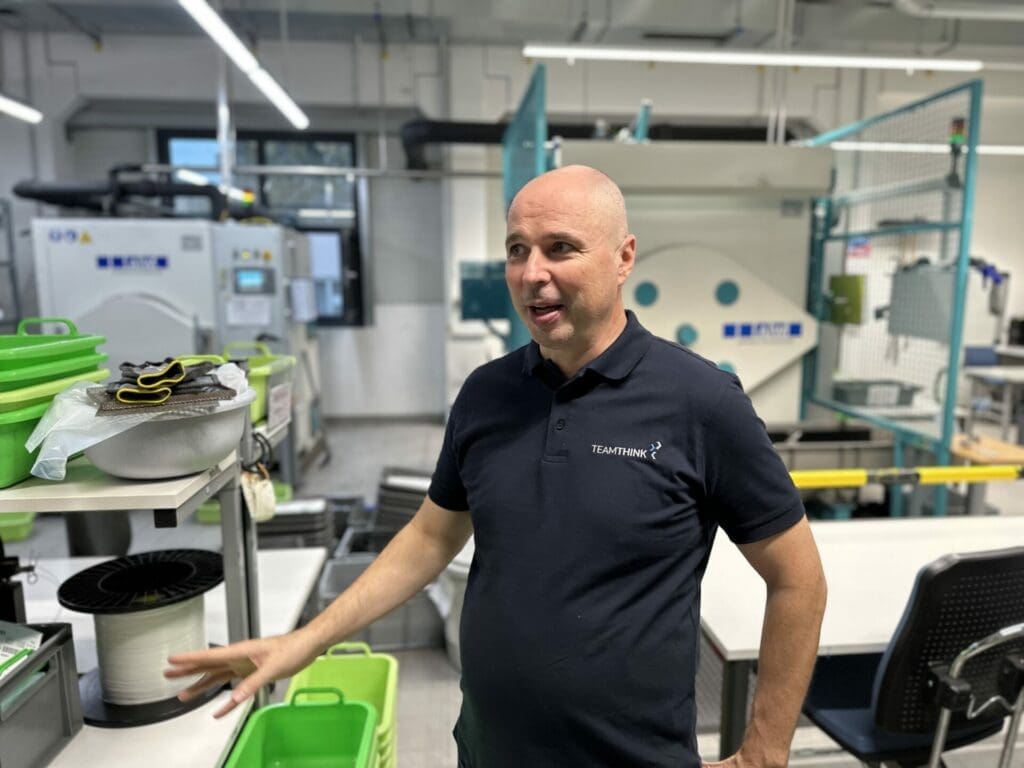
Wertstromanalyse – zentrale Methode
Die Wertstromanalyse (WSA) (Eng. VSA=Value Stream Analysis) ist die zentrale Methode in der Lean Beratung. Die Kernwertschöpfungsprozesse werden einer Analyse unterzogen mit dem Ziel, Verschwendung zu reduzieren oder zu eliminieren um die Durchlaufzeit zu reduzieren. Ziel ist es über ein neues Wertstromdesign (Eng. VSD=Value Stream Design) einen optimaleren Prozess zu entwickeln.
Die Wertstromanalyse wird auch deshalb als zentrale Methode gesehen, weil die Kunden als auch die Lean Berater das Unternehmen darüber genau kennenlernen. Eine Wertstromanalyse ist in der Regel der Startpunkt für eine längere Lean Transformation. Wertstromanalysen werden später immer wieder wiederholt, um noch mehr Verschwendung im Prozess zu eliminieren.
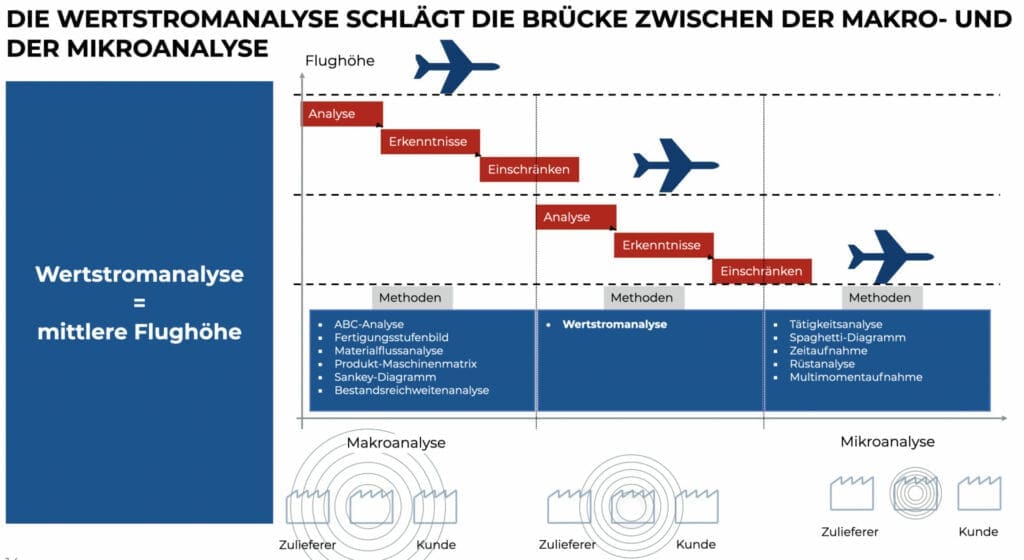
Eine Wertstromanalyse schlägt die Brücke zwischen der Makro- und der Mikroanalyse eines Unternehmens. Wertstromanalysen versuchen dabei die Realität des Wertstroms möglichst gut abzubilden. Es handelt sich dabei um eine Annäherung an die Realität. Keine Wertstromanalyse kann die Realität perfekt abbilden, da sich die Realität ständig ändert. Es handelt sich also nicht um eine harte Wissenschaft, da wir immer nur eine Momentaufnahme des Unternehmens betrachten, aufnehmen und analysieren können.
Eine annäherungsweise Erfassung des gesamten Wertstroms reicht aus, um die Kernprobleme im Wertstrom zu erfassen und Gegenmaßnahmen zu ergreifen.
Die Detailanalysen und Detaillösungen können punktuell, nachgelagert in KAIZEN Workshops erfolgen.
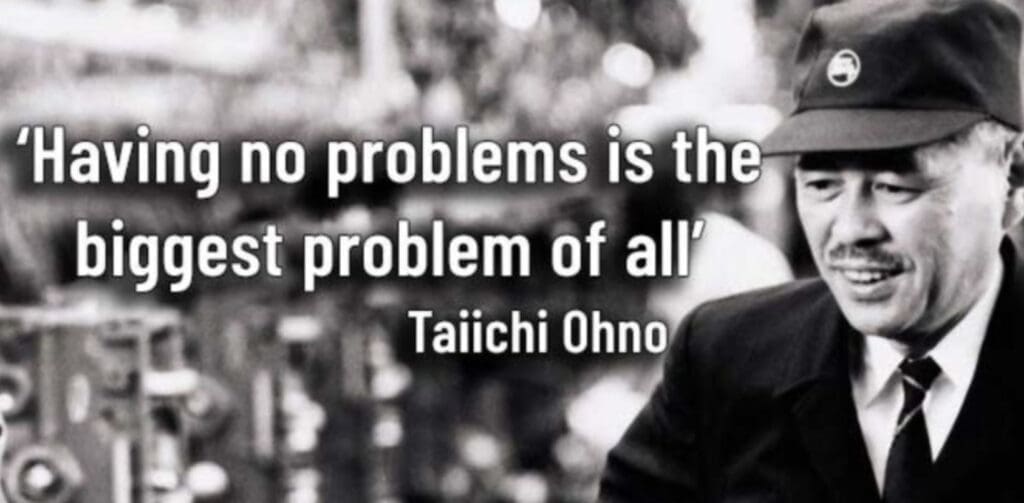
Eine Wertstromanalyse erzeugt vollständige Transparenz
Eine Wertstromanalyse ist eine positive Lernerfahrung für die Teilnehmer, da wir Lean Management in der Praxis erleben können. Die Lean Prinzipien und Werkzeuge werden an einem konkreten Wertstrom angewandt und erzeugen sofort Ergebnisse.
Eine Wertstromanalyse kann für die Beteiligten eine schwierige Erfahrung sein, weil alle Herausforderung im Wertstrom transparent werden.
Wir nutzen diese neue Transparenz dafür, um in der Zukunft eine Verbesserung zu erreichen und gehen nicht auf die Suche nach Schuldigen. Das wäre Verschwendung. Mitarbeiter versuchen immer im Interesse des Unternehmens beste Ergebnisse zu erreichen – in der Vergangenheit, in der Gegenwart und in der Zukunft.
Die Rolle der Beratung ist es einerseits Transparenz zu erzeugen und die Herausforderungen herauszuarbeiten, denn ohne Transparenz kann kein Fortschritt erzielt werden. Andererseits würdigen die Berater das Kundensystem für seine bisherigen Lösungswege.
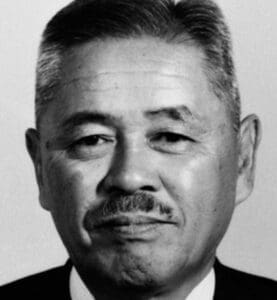
„Es kann kein Fortschritt erzielt werden, wenn wir uns mit der aktuellen Situation zufrieden geben. “
– Taiichi Ohno
Der Workshop: Wertstromanalyse & -design
Nachfolgend wird ein typischer Wertstromanalyse & -design Workshop beschrieben. Ein Workshop dauert in der Regel 5 Tage und folgt dieser Agenda:
Montag | Dienstag | Mittwoch | Donnerstag | Freitag |
Start | Morgenrunde | Morgenrunde | Morgenrunde | Morgenrunde |
Grundlagen Lean | Produkt/Prozess Matrix | Kalkulation Flussfaktor / DLZ | 5 Lean Prinzpien | Berechnung der Kosteneinsparungen |
Gemba Walk | Wertstromaufnahme – Prozessfluss | Kaizen Blitze | Wertstromdesign | Lean Masterplan |
Definition der Hausforderungen | Wertstromaufnahme – Materialfluss | Analyse der Kostenstruktur | Definition der Lean Projekte | Nächste Schritte |
Lean Analye Methoden | Wertstromaufnahme – Informationsfluss | Weitere Analysen* | Benchmark Lösungen | Abschluss |
Abschluss | Abschluss | Abschluss | Abschluss |
*Rüstzeit Analyse, Spaghetti Diagramm, Kreidekreis, Multi-Moment-Analyse, etc.
Ziele des Workshops
- Aufnahme des Wertstroms
- Herausarbeiten der Herausforderungen
- Ableiten des neuen Wertstromdesigns
- Einen Lean Masterplan mit definierten Teilprojekten vereinbaren
- Abschätzen der Kosteneinsparungen pro Teilprojekt
- Weiterbilden der Teilnehmer des Workshops in wichtigen Lean Konzepten
Wertstrom Analyse und Design – Tag 1
Am Tag 1 der Wertstrom Analyse geht es erst einmal sich gegenseitig Kennenzulernen und darum Basiswissen über Lean Management zu vermitteln.
Die Berater leiten her, warum Veränderung überhaupt notwendig ist und erklären das Q-K-L-Dreieck und das Lean Haus mit seinen verschiedenen Aspekten.
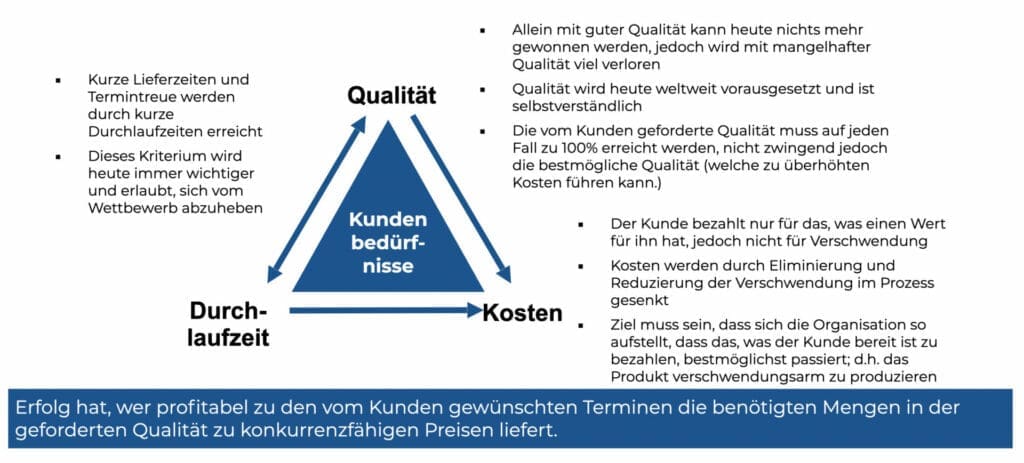
Das Q-K-TLDreieck sagt im wesentlich aus, dass Unternehmen erfolgreich sind, wenn Sie dem Kunden das Produkt zum gewünschten Termin in der benötigten Mende und Qualität zu einem konkurrenzfähigen Preis liefern. Insbesondere der Zusammenhang zwischen Beständen und Durchlaufzeit wird thematisiert und schließlich hergeleitet, dass wir im Lean Management über die Verkürzung der Durchlaufzeit stetige Verbesserungen erzwingen und erzeugen.
Das Lean Haus basiert im Wesentlichen auf den zwei Pfeilern des Toyota-Produktionssystems.
Das Konzept Just-in-Time umfasst die Prinzipien von Takt, Ein-Stück-Fluss, Sog/Kanban und das Konzept von schnellen Werkzeugwechseln (SMED).
Das Konzept Jidoka umfasst die Prinzipien der 0-Fehler Strategie, Qualität im Prozess, Intelligent Automation oder Autonomation mit sofortigem Stop der Produktion sowie Poka-Joke und PDCA-Zyklus für strukturierte Problemlösungen.
Die Basis des Lean Hauses sind Arbeitssicherheit, Ordnung und Sauberkeit, Standardarbeit und visuelles Management. Auf dieser Basis kann Stabilität durch Total Productiv Maintenance (TPM) und geglättete und nivellierte Produktion (Heijunka) entstehen.
Der Status Quo wird immer wieder durch weitere Reduzierung von Verschwendung und Prozessverbesserung, Coaching im Prozess, Prozessanalysen und etabliertes Shopfloor Management optimiert.

Als weiteres wichtiges Element wird das Konzept von Muda (Verschwendung), Muri (Überbelastung) und Mira (Unausgewogenheit) erklärt. Die 7 Arten der Verschwendung sind in der Regel oft schon bekannt und werden nochmals an Beispielen hergeleitet.
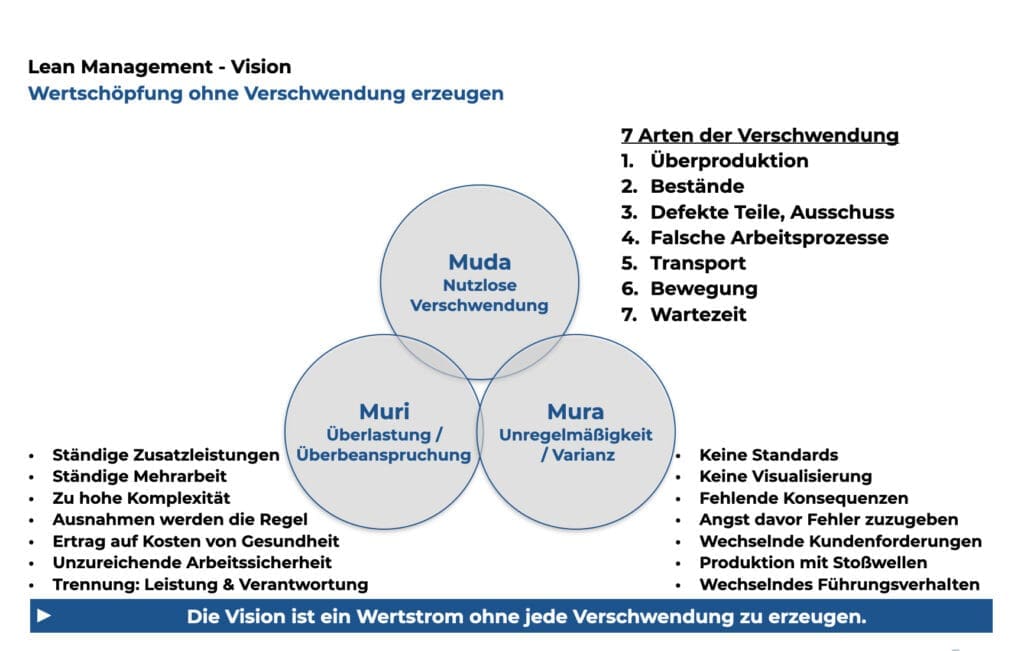
Am Nachmittag geht die Gruppe sensibilisiert mit dem neuen Wissen dann natürlich auf den Shopfloor zum Gemba Walk. Das Ziel des ersten Gemba Walk ist es den Prozess zu verstehen und Verschwendung/Herausforderungen zu definieren.
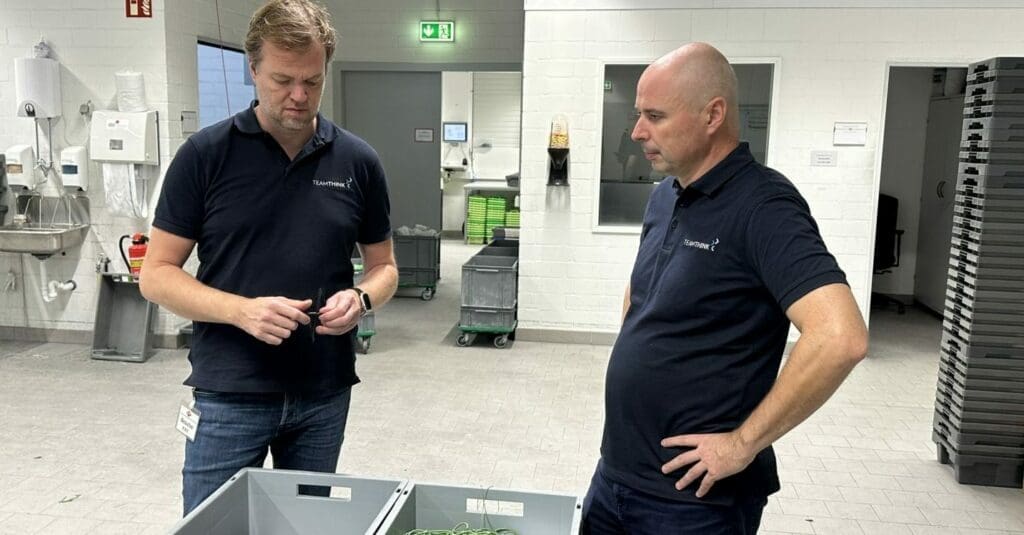
Die Beobachtungen werden anschließen gemeinsam in der Gruppe gesammelt und visualisiert und im Team diskutiert. So entsteht ein gemeinsames realistisches Verständnis von der Situation und der erste Tag endet.
Wertstrom Analyse und Design – Tag 2
Nach einer Morgenrunde, in der wichtige Aspekte des Vortages noch einmal reflektiert werden analysieren die Berater die Produkt/Prozess Matrix und entscheiden gemeinsam mit dem Kunden über die Auswahl der Wertströme welche betrachtet werden.
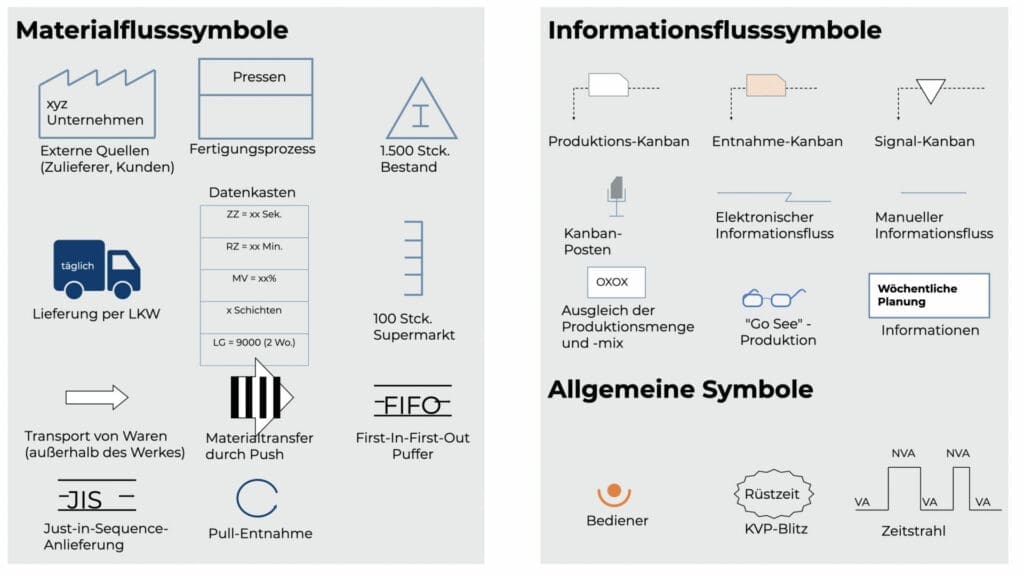
Jetzt geht es los und die Wertstrom-Analyse kann starten. Mit Hilfe von standardisierten Symbolen bilden wir den Prozessfluss im Wertstrom mit der Hilfe von Post-Its ab.
Wir erfassen die Kundenanforderungen berechnen den Kundentakt und zeichnen das Kundensymbol ein. Wir zeichnen die Prozessschritte und Bestandsdreiecke ein und ermitteln die die Zykluszeiten und Prozesszeiten.
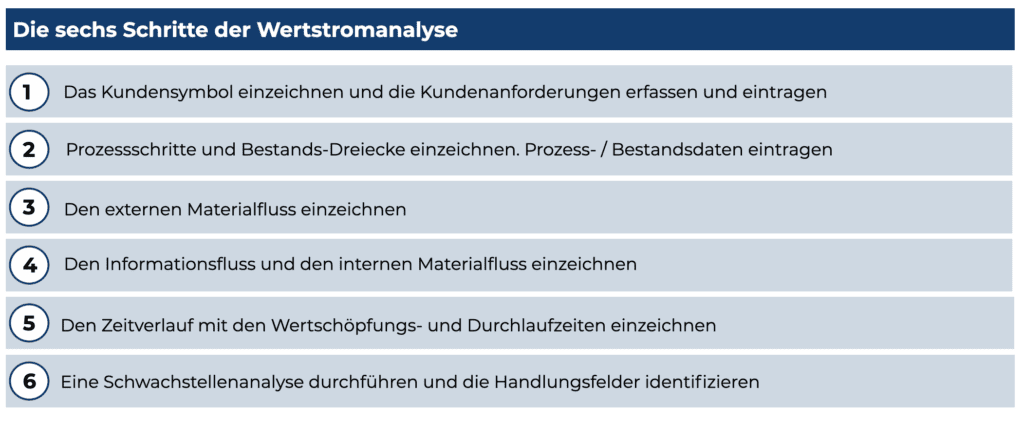
Das Team holt sich die notwendigen Daten aus dem ERP-System heraus oder geht auf die Gemba und misst die Zeiten manuel nach. Schließlich werden Mitarbeiter und Schichtzeiten ergänzt und das Team berechnet die Ressourcen.
Dann geht es wieder auf die Gemba, um für den Materialfluss die Bestände im Prozess zu zählen. Wir ermitteln so die Wartezeit zwischen den Prozessschritten.
Schließlich wird noch der externe und interne Materialfluss und der Informationsfluss zur Produktion ausgehend von der Kundenbestellung ergänzt. Das Team berechnet aus den ermittelten Daten die Durchlaufzeit und den Flussgrad, der sich aus der Wertschöpfungszeit , der Zykluszeit und den Wartezeiten ableitet.
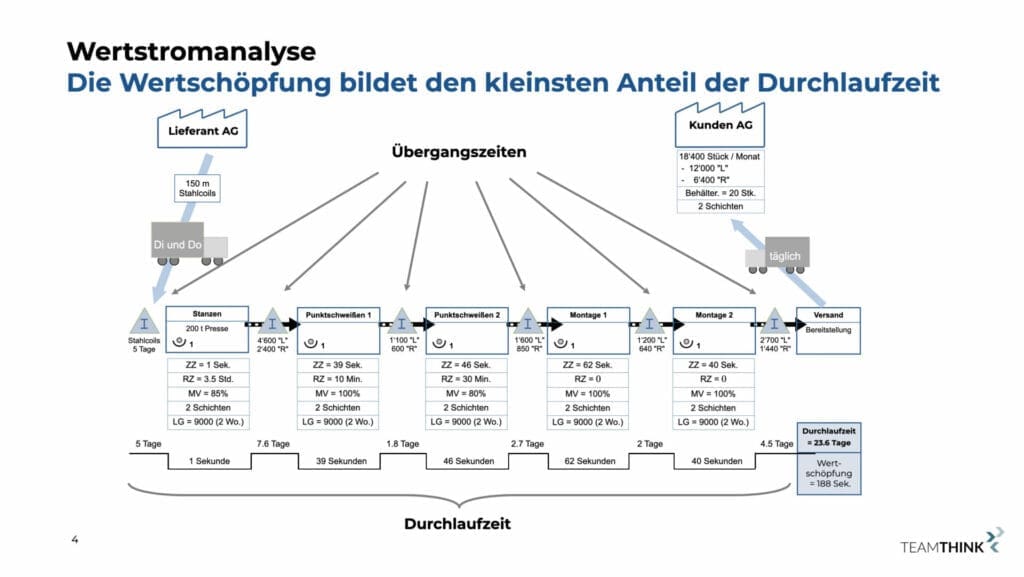
Der Prozess der Wertstromaufnahme bewirkt im Team einen wichtigen Prozess der Teamentwicklung. Die Teilnehmer lernen die Lean Denkweise in der Praxis und sehen das große Einsparungspotential im Prozess!
Gleichzeitig erlebt das Team immer wieder Momente der Ernüchterung, da die Realität im Unternehmen sichtbar wird.
Wertstrom Analyse und Design – Tag 3
Nach einer Morgenrunde analysieren wir die Kostenstruktur im Wertstrom. Alle Daten und relevante KPIs des Unternehmens liegen nun vor.
Im nächsten Schritt definiert das Team die Verbesserungspunkte im Wertstrom. Kaizen-Blitze kennzeichnen wo es im Wertstrom Handlungsbedarf gibt.
Die Berater erklären verschiedene Werkzeuge für Detailanalysen wie z.B. Rüstzeit Analyse, Spaghetti-Diagramm, Kreidekreis, Multi-Moment-Analyse.
Das Team führt diese Detailanalysen an bestimmten Punkten auf dem Shopfloor durch, um einen noch besseren Überblick zu bekommen. Die Ergebnisse werden zusammen besprochen.
Nun ist die Wertstromanalyse abgeschlossen und der schwierigste Teil der Woche liegt hinter uns. Wir haben ein klares Bild der Gesamtsituation und volle Transparenz. Einerseits sieht das Team das große Verbesserungspotential. Andererseits herrscht etwas Ernüchterung: wir könnten noch so viel besser sein!
Alle Teilnehmer des Workshops gehen jetzt mit völlig neuen Augen über den Shopfloor. Sie haben „sehen gelernt“. Die Teilnehmer erkennen überall die Verschwendung im Prozess.
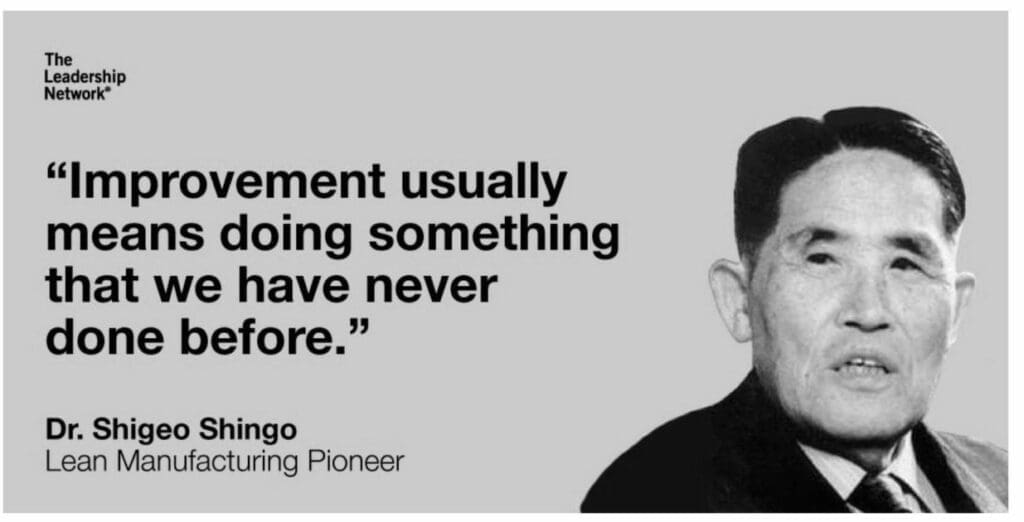
Der dritte Tag endet mit der Erkenntnis, dass es noch viel Raum für Verbesserung gibt. Die Teilnehmer sind gespannt auf den nächsten Tag, an dem das neue Wertstromdesign entwickelt werden soll.
Wertstrom Analyse und Design – Tag 4
Nach der Morgenrunde liefern die Berater als Vorbereitung für das Wertstromdesign einen Input zu den 5 Leanprinzipien.
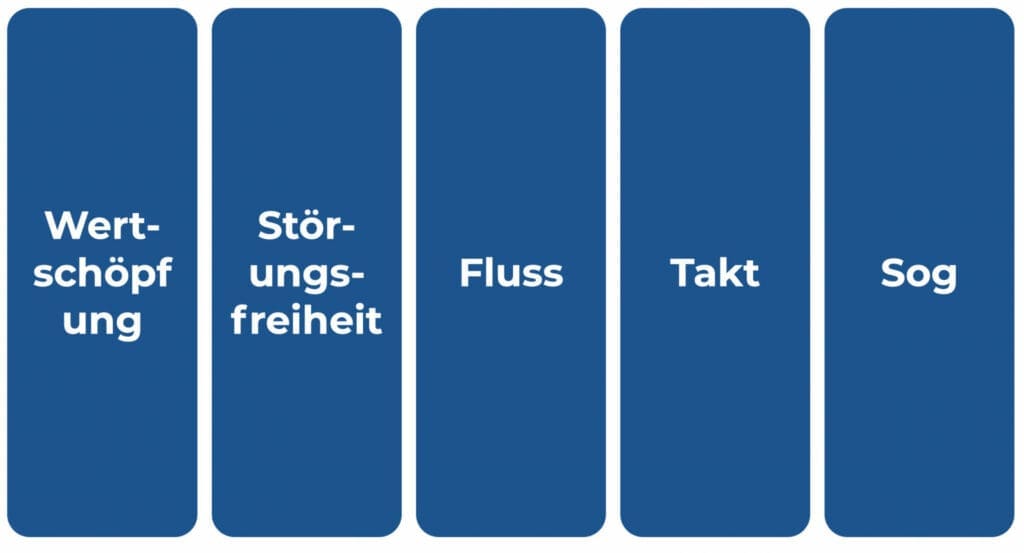
Da die Prinzipien der Wertschöpfung und Störungsfreiheit bereits an den Vortagen besprochen wurden, widmen wir uns intensiv den Themen Fluss und Verkettung im Wertstrom (Chaku-Chaku-Prinzip) sowie Nivellierung und Glättung der Produktion auf der Basis des Kundentakts (Heijunka). Schließlich wird noch die Sog/Pull Produktion mit Hilfe von Kanban Systemen thematisiert.

Nach einer Pause geht es an die Arbeit. Die Gruppe setzt das gelernte Wissen mit Hilfe der Berater auf der Basis der 7 Leitlinien für das Wertstromdesign um und konzipiert den neuen Wertstrom. Die Gruppe ist energiegeladen. Sie erkennt das Potential und umsetzbare Lösungen!
Nach einigen Interrationen liegen jeweils zwei Szenarien für das neue Wertstromdesign vor: eine konservatives neues Design und ein radikales Design.
Der Durchbruch ist gelungen. Mit diesem neuen Wertstromdesign sind wir in der Lage die Durchlaufzeit beeindruckend zu reduzieren!
Das Team ist begeistert und diskutiert die Möglichkeiten die sich aus dem neuen Wertstrom ergeben. Die Umsetzung in die Realität wird geprüft und geplant.
Für die Umsetzung des Wertstromdesign in die Realität und ausgehend von den aktuellen Herausforderungen im Wertstrom, leitet die Gruppe nun im nächsten Schritt die relevanten Teilprojekte im Rahmen der Lean Transformation ab. Nach einer intensiven Diskussion entsteht eine Liste von 10 hoch relevanten Lean Projekten.
Abschließend nutzen wir das Know how der Gruppe und erstellen eine Sammlung von Best-Practice / Benchmark Lösungen für ausgewählte Themen und schließen den Tag ab.
Wertstrom Analyse und Design – Tag 5
Nach der Morgenrunde befasst sich die Gruppe mit den Ergebnissen der Multi-Moment-Analyse.
Während der 5 Tage Workshop war einer unser Berater im Team zu unterschiedlichen Zeitpunkten auf dem Shopfloor und erfasste insgesamt an ca. 10 Messzeitpunkten die Produktivität der Maschinen in den relevanten Wertströmen. Der Berater erfasste punktuell die Laufzeit, Rüstzeit oder Stillstandszeit aus anderen Gründen.
Aus diesen punktuellen Werten schätzen die Berater die Gesamtanlageneffizienz (GEA\OEE) in relevanten Bereichen ab. Auch wenn es sich nicht um vollständig belastbare Werte handelt, ist die so ermittelte GEA ein guter Indikator für die Effektivität der Anlagen. Die Gruppe diskutiert die Ergebnisse und ist erstaunt, dass die Abschätzung mit der Realität recht gut übereinstimmt.
Noch einmal mehr wird der Handlungsdruck im Unternehmen deutlich. Es ist nun allen Teilnehmer klar geworden. Wir müssen etwas ändern!

Im nächsten Schritt entwickelt das Team in Kleingruppen je eine Projektcharter für die am Vortag definierten Teilprojekte. Es werden Arbeitspakete, Meilensteine, Laufzeit und Zieltermin, das Projektteam und die Projektleitung der Teilprojekte definiert.
Dann berechnet das Team noch überschlägig die Kosteneinsparungen, die pro realisiertem Teilprojekt erreicht werden können. Es wird klar, dass sich durch die Projekte eine erhebliche Reduzierung der Kosten realisieren lässt.
Zum Abschluss der 5 langen Tagen werden noch einmal alle Teilprojekte in einem Lean Masterplan zusammengefasst und kritisch auf realistische Umsetzung geprüft.
Das Team ist erschöpft aber auch zufrieden. Sie sehen Ihr Unternehmen mit neuen Augen und sind begeistert von der intensiven Lernerfahrung.
Implementierungsphase
Nach dem Workshop geht es in die Implementierungsphase. Dazu erfolgt im nächsten Schritt die Entwicklung und Visualisierung eines taktischen Implementierungsplan (TIP) und Wochenplan (WP) und Kennzahlen zur konsequenten Überprüfung des Fortschritts in der Lean Transformation.
An dem Ort der Visualisierung findet die Regelkommunikation für die Lean Transformation mit dem Changeteam / Treiberteam der Lean Transformation statt.
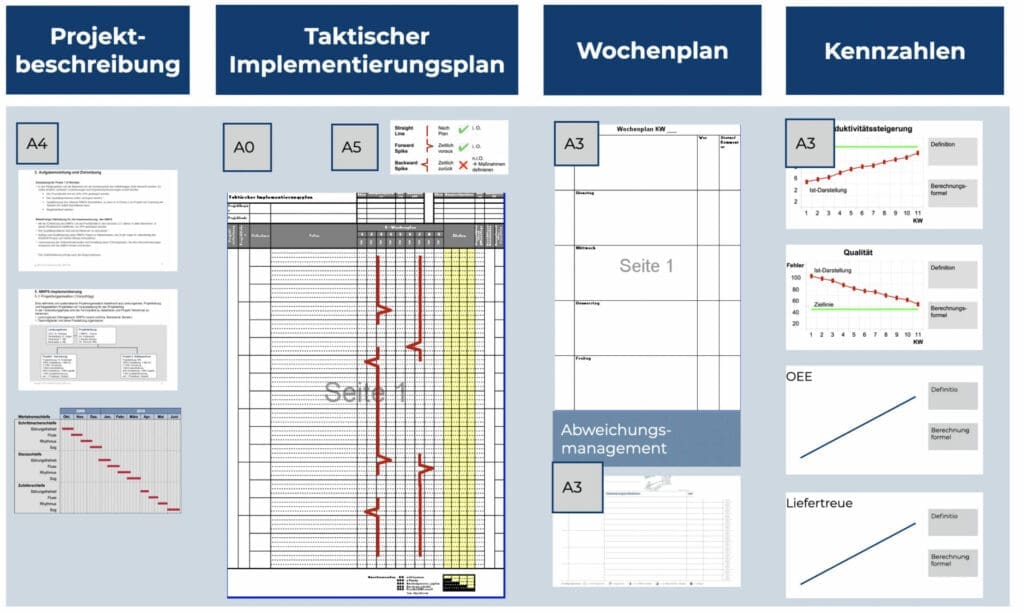
TEAMTHINK – Spezialist für Lean Transformation & Führungskulturwandel
Eine Lean Transformation geht immer mit einer Entwicklung der Führungskultur im Unternehmen einher.
TeamThink – International Business Consulting ist Spezialist für Lean Transformation und Führungskulturwandel.
Wir unterstützen unsere Kunden einerseits auf dem Weg zur operativen Exzellenz auf der Basis von Lean Management.
Anderseits liefern wir aus einer Hand die notwendigen Führungstrainings und den Kulturwandel im Führungsteam.
Unsere Kunden bekommen so die gesamte Transformation gut abgestimmt zueinander aus einer Hand.

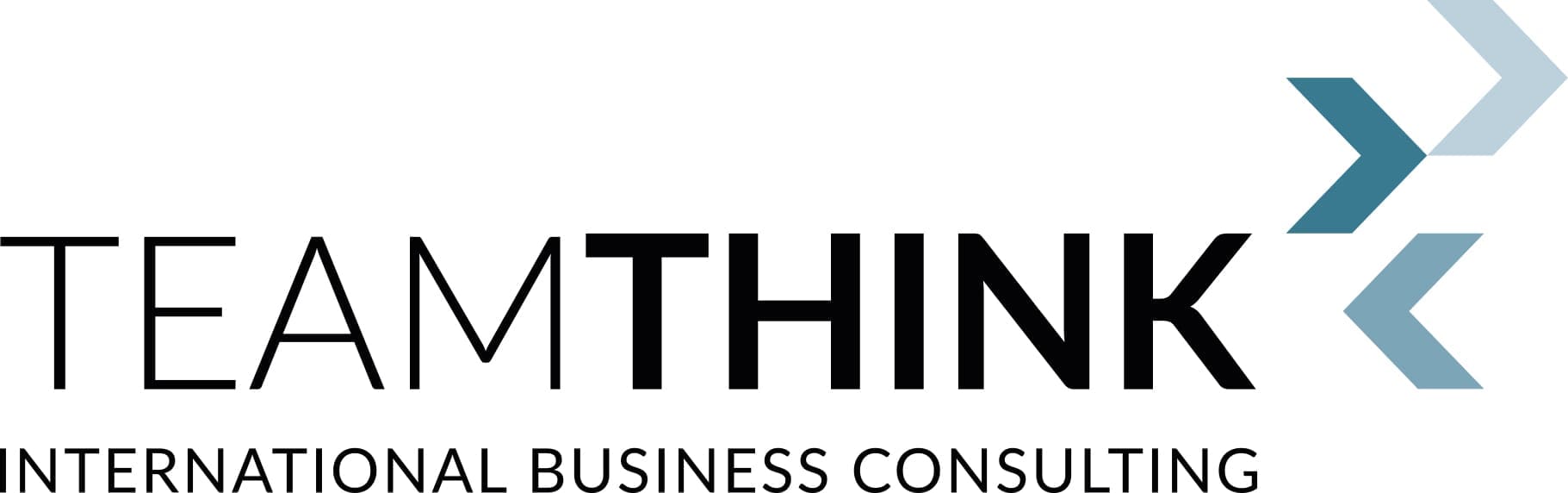
Contact us now!
We have more than 20 years of experience and deliver high quality consulting for your Agile, Lean or Digital Transformation.