Lean Production System (LPS)
“The Toyota Way” ushers in an era
In 2003, “The Toyota Way” written by Jeffrey Liker was published, one of the best selling books on the Lean Production System. Alongside the book “The Machine That Changed the World” by Womack, Jones and Roos, the book The Toyota Way is standard reading for every manager and consultant and ushered in the era of lean management worldwide.
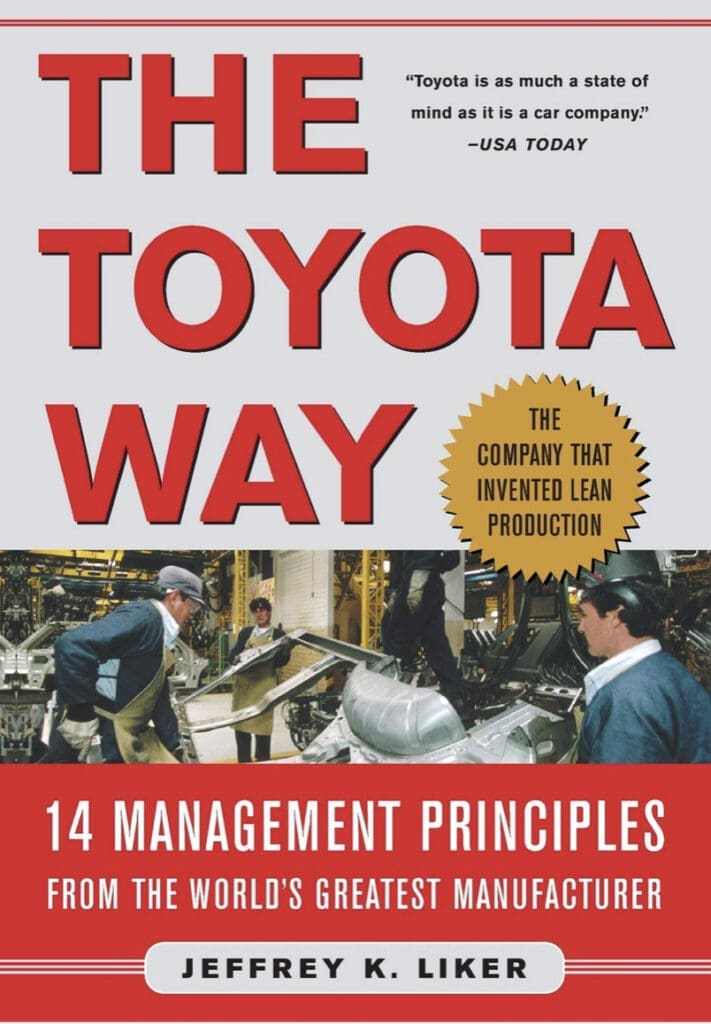
The Lean Management System has been in existence for more than 70 years, and is largely known through the Toyota company.
For about 30 years, business leaders (“Japan travels”) from all over the world have regularly made pilgrimages to Japan to experience first-hand the Lean Production System.
For the past 20 years, lean management and its tools have been an integral part of corporate cultures worldwide.
“Why is that?” you may ask. The answer is simple and compelling:
Lean Production System (LPS) is the most successful system for company management to achieve cost reduction by increasing productivity, while highly satisfied customers receive highest quality goods with highest delivery punctuality at the best price and highly motivated employees are engaged in value creation under optimal conditions of work safety.
The fascination with Lean Production System (LPS)
The fascination with the Lean Production System is best summed up in the following quote from Jeffrey Liker, which expresses well that the Lean Production System is not a collection of effective management tools, but rather an ethical approach to life that combines the pursuit of continuous (self-)improvement with the highest standards of performance.
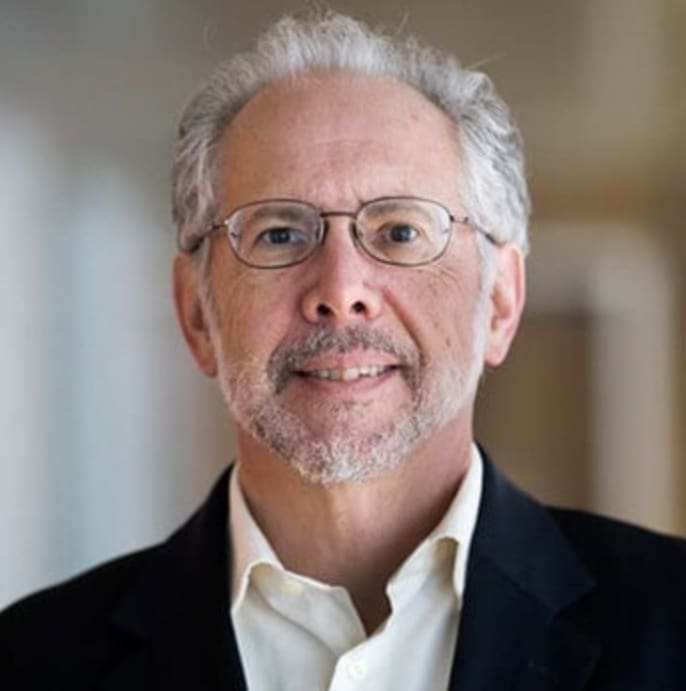
„Toyota is as much a state of mind, as it is a car company.“
– Jeffrey Liker
The contest has been decided
From the perspective of industrial history, the contest for the better production system has been decided between the FORD production system optimized for mass production (batch production) and machine utilization and the Toyota production system optimized for waste avoidance and optimal flow (one-piece flow).
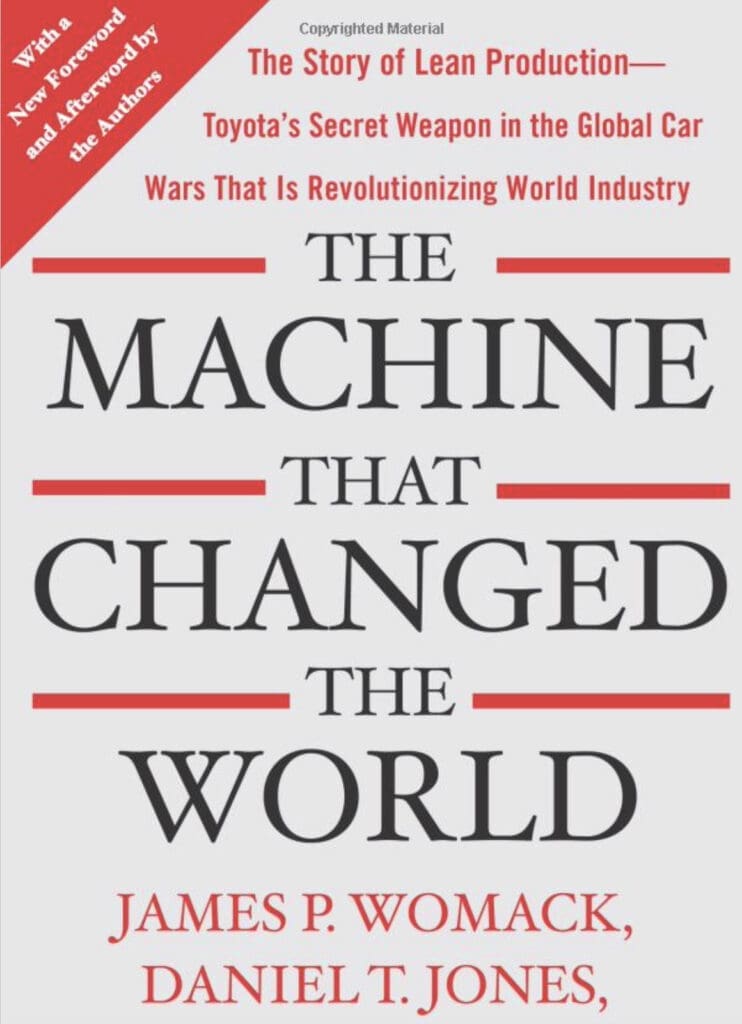
The Lean Production System (LPS) has clearly won this competition. More or less all renowned companies in the world now use the LPS to achieve their own goals.
While in the USA (“The Land of the plenty”) in the postwar period (WW II) an abundance of material, employee and capital resources prevailed and the car manufacturer FORD optimized its production process for machine utilization and mass production, quite different conditions prevailed in Japan.
The defeated war party plagued Japan with a chronic shortage of materials, employees and capital. In these adverse circumstances, the Toyoda family, known for the production of looms, decided to invest in the development and manufacture of automobiles.
From the beginning, the avoidance of waste and the focus on a cost-effective, optimal production manufacturing process were core elements of the Toyota Way. Time and again, ways were sought to get the most out of materials and employees with as little capital expenditure as possible in production.
This is how the concept of “Low Cost Intelligent Automation” came about. The aim is to achieve the simplest possible technical solutions for automation in the production process. The aim is to keep fixed costs (machines) as low as possible and to react to increasing or decreasing demand with variable costs (employees).
A distinction is made between the production of things (monozukuri) and the shaping of people (hitozukuri). The LPS places strong emphasis on the development of employees because, unlike inanimate machines, people want to learn and develop constantly.
In the wake of the oil crisis in the early 1970s, Toyota advanced to become the world leader in automobile manufacturing within a few years due to its production cost advantage, while American and European automakers struggled with high production costs and declining sales.
Production cost advantage
In any market, the price level for products is decreasing while costs are continuously increasing. The market and customers want to pay steadily lower prices for an innovative product (with best quality and delivery time) and the owners and employees demand steadily higher profits and increasing salaries.
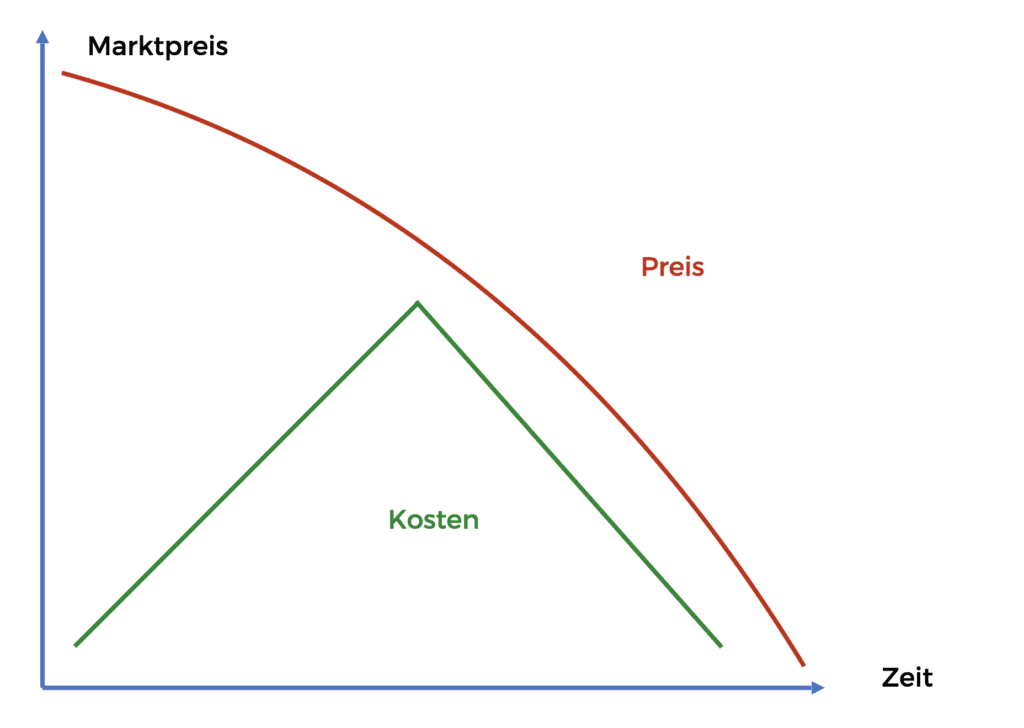
By implementing LPS, companies are still gaining production cost advantages. Because every company is confronted with the conflict between rising costs and falling prices and is forced to reduce costs and constantly increase productivity.
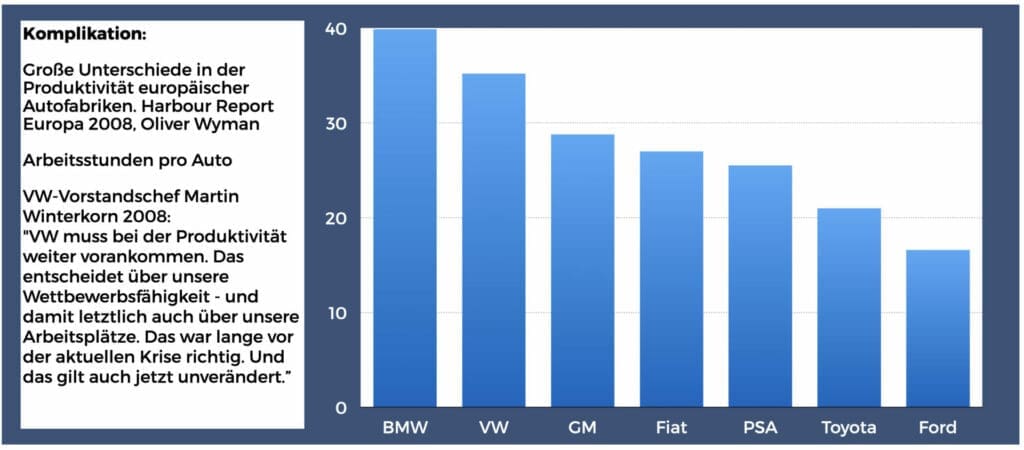
For example, a 2008 study by the consulting firm Oliver Wyman shows the still large differences in productivity (hours worked per car) in the global automotive industry.
Ohno Taiichi – father of the Toyota-Production system
The Toyota Production System was significantly developed by Ohno Taiichi (February 29, 1912 – May 28, 1990). He is considered the father of the Toyota Production System and was the principal architect of Toyota’s post-World War 2 reconstruction. He started as a production engineer in 1943 and retired as a Toyota Executive in 1978.
Under his leadership, the 7 types of waste (muda in Japanese) and the concepts of just-in-time, jidoka, flow, pull, and kanban and supermarket systems were developed based on standard processes.
From Taiichi Ohno also comes the famous statement, “Without standards, there can be no improvement at all.” In essence, this phrase expresses how important the constant and relentless drive for improvement in process was to Ohno.
It was not until after his retirement in 1978 that he was persuaded to formally write down the management system and related principles that had developed under his leadership. He wrote several books about this system, including Toyota Production System: Beyond Large-Scale Production.
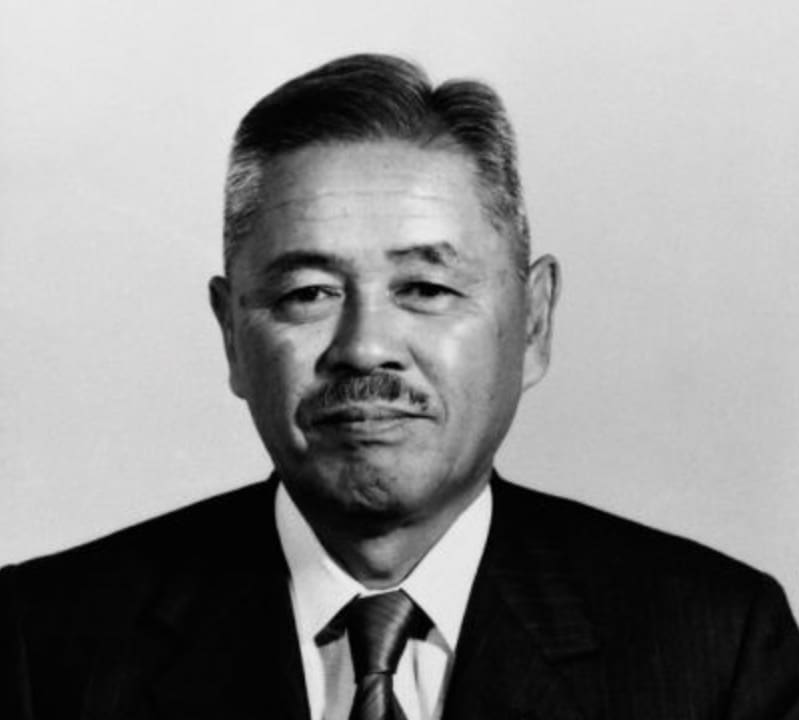
„Having no problems is the biggest problem of all. Progress cannot be generated, when we are satisfied with the current situation.“
– Taiichi Ohno
The Lean House
The Lean House is a schematic overview in which the essential core elements of the LPS are presented in a graphic. The “roof” forms the strategy, goal and leadership model. The “roof” is supported by the two pillars “Just-in-Time Production” and “Jidoka/Autonomation”. “Problem Solving” and “Continuous Improvement” are built on the foundation “Basis of Cooperation”.
The individual elements are briefly explained below. For a complete explanation of the individual elements, we recommend the literature mentioned.
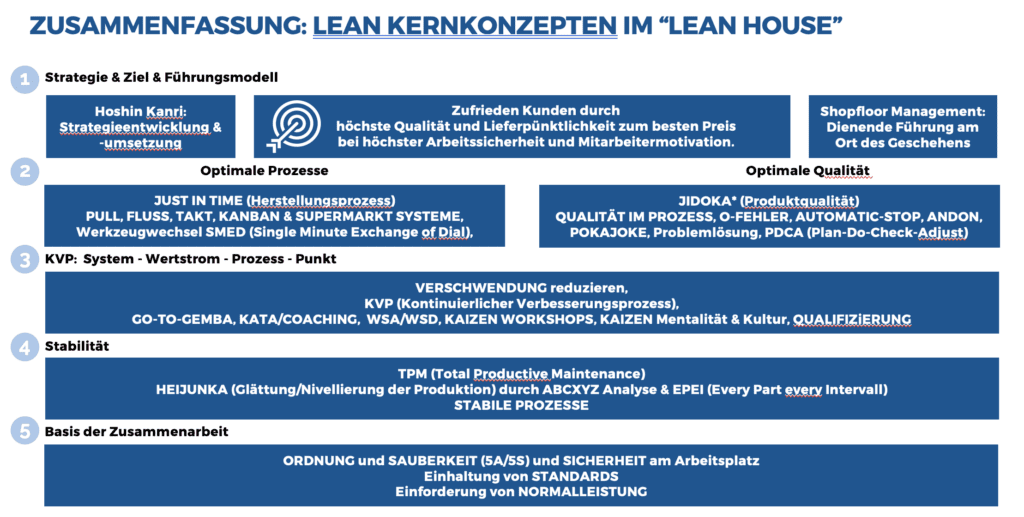
Strategy, Goal and Leadership model
The overriding goal in the LPS is satisfied customers who are convinced by the highest quality and delivery punctuality at the best price, while highly motivated employees work under optimal conditions of occupational safety in the value creation.
In an annually repeated strategy development process (Hoshin Kari), goals between all areas are derived and harmonized via a so-called X-matrix and goal conflicts are reduced.
The daily operational achievement of goals and the control of deviations at the point of value creation is ensured by setting up a cascade of standard communication. Central to this is the mind-set of “serving leaders” of the managers. Managers see themselves as enablers and problem solvers and drivers of continuous improvement in the sense of the value stream.
Manufacturing process and product quality
At its core, LPS is about reducing waste in the value creation process by realizing the principles of “just-in-time” (the right part at the right place at the right time) and “Jidoka” (automation with a human touch).
The manufacturing process (JIT) is based on the principles of pull, flow and takt, and material flows are controlled at the lowest possible inventory levels via self-regulating autonomous control loops using Kandan cards. If necessary, inventory is built up in so-called material supermarkets to ensure a continuous production process.
Product quality is ensured by ideally stopping production automatically (Automatic Stop) or by humans during production when deviations or errors occur.
Employees on the line were instructed to stop production (“pull the line”) when problems arose in production. A team of skilled workers and foremen would then first solve the problem so that the line could start up again, and then investigate the root cause of the problem to eliminate it permanently.
The quality mentality is aptly expressed in the slogan “Build-in-Quality.” Only good quality is accepted in the next process step. Only good quality is produced and passed on. In case of deviations, production is stopped.
Andon systems (light signals) indicate to the foreman in the production hall which workstation is currently experiencing problems. Tools and machines optimized for problem and accident prevention (Pokajoke) ensure fail-safe production.
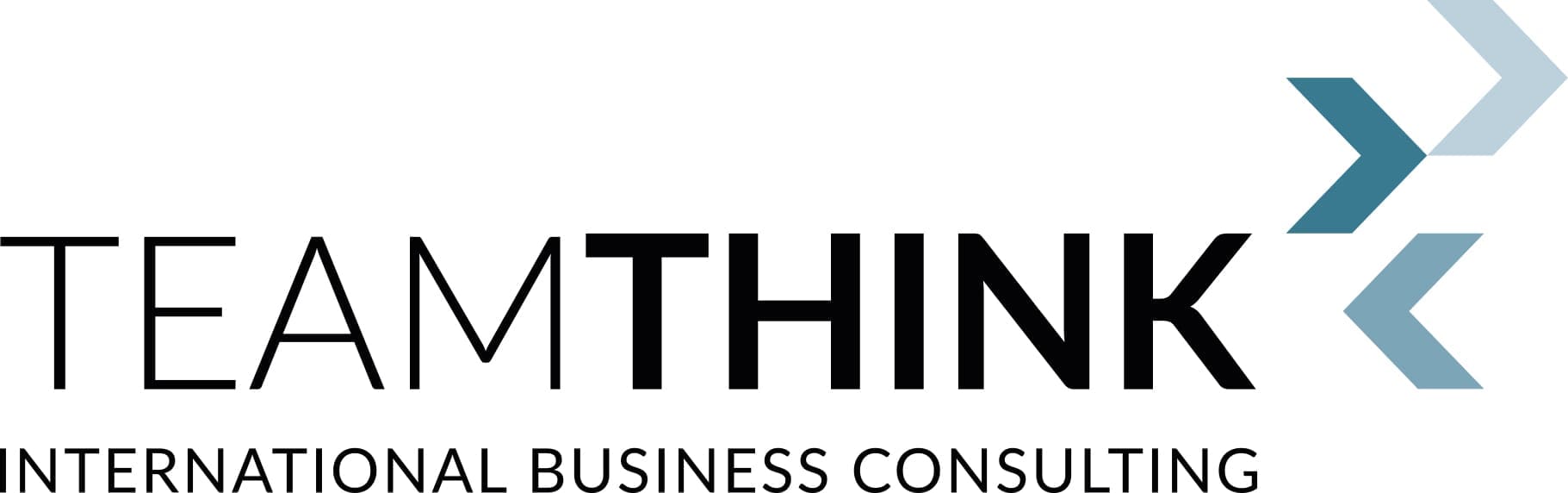
Contact us now!
We have more than 20 years of experience and deliver high quality consulting for your Agile, Lean or Digital Transformation.
Problem solving
Strukturierte Problemlösung von immer wiederkehrenden Problemen ist eine besonders schwierige und wichtige Disziplin im LPS.
Wir unterscheiden leichte Probleme, die sofort vom Mitarbeiter oder Meister gelöst werden können. Im Fokus liegen mittelschweren Problemen, die mit etwas Aufwand (z.B. PDCA Zyklus oder Kaizen Workshops) gelöst werden können. Außerhalb des Fokus liegen seltene schwerwiegende Probleme, die nur mit hohem Aufwand gefunden und behoben werden können (z.B Six Sigma).
Im letzten Fall sind externe Berater oder Experten zu beauftragen. In den ersten beiden Fällen geht es darum die Problemlösekompetenz im Unternehmen aufzubauen.
Eine wesentliche Methode ist die Optimierung von Werkzeugwechsel (SMED, Single Minute Exchange of Dual), um die Effektivität in der Produktion zu erhöhen und die Durchlaufzeiten zu reduzieren.
Schließlich gilt es in jeder Produktion die Auslastung von Mensch und Maschine durch Nivellierung und Glättung zu optimieren. Unter dem Stichwort Heijunka finden sich recht komplexe Analyemethode wie ABC / XYZ und EPEI-Analyse. Richtig angewandt führen Sie zu einer erheblichen Verbesserung in den Produktionsabläufen.
Structured problem solving of recurring problems is a particularly difficult and important discipline in LPS.
We distinguish light problems, which can be solved immediately by the employee or foreman. In focus are difficult problems, which can be solved with some effort (e.g. PDCA cycle or Kaizen workshops). Out of focus are rare very difficult problems, which can be found and solved only with high effort (e.g. Six Sigma). In the last case, external consultants or experts must be engaged. The aim is to build up problem-solving competence within the company for the first two cases of problems.
An essential method is the optimization of tool changes (SMED, Single Minute Exchange of Dual) in order to increase the effectiveness in production and reduce lead times.
Finally, in any production it is necessary to optimize the utilization of man and machine by leveling and smoothing the production load. Under the keyword Heijunka you can find analysis methods like ABC / XYZ and EPEI analysis. Applied correctly, they lead to a significant improvement in production processes.
Continuous Improvement
Das Kai-Zen Konzept ist die grundlegende Haltung im LPS und mittlerweile Allgemeinwissen im Industriekontext. Wie das genannte Zitat von Taiichi Ohne deutlich macht ist diese Haltung absolut zentral für das Verständnis von LPS.
Allerdings gibt es laut Jun Nakamuro Übersetzungsfehler, die richtig gestellt werden sollen.
KAIZEN meint eigentlich das kontinuierliche Streben nach Selbstverbesserung auf der Grundlage der Überzeugung, dass jeder Mensch sein Leben einsetzen sollte, um andere Menschen zu unterstützen (HANSEI).
Erst durch den individuellen Anspruch an die stetige Selbstverbesserung entsteht im Ergebnis eine Veränderung in der physischen Welt in Prozessen, Technik oder Werten. (KAIRYO)
Was wir im allgemeinen unter KAIZEN verstehen, ist in der Regel der kontinuierliche Verbesserungen Prozess (KVP) in der physischen Welt. Mitarbeiter beobachten Fakten am Ort des Geschehens und bringen Idee für Verbesserungen ein, die sorgfältig nachverfolgt werden. Der KVP basiert aber auf die oben genannte eine Haltung und Einstellung zugrunde gehen.
Ich denke alleine an dieser detaillierten Aufgliederung des KAIZEN Begriffs können wir erkennen, welche zentrale Rolle diese Einstellung gegenüber den sich selbst und dem Arbeitgeber und der Umwelt im LPS spielt.
The Kai-Zen concept is the fundamental attitude in LPS and is now common knowledge in the industry context. As the above quote from Taiichi Ohne makes clear, this attitude is absolutely central to the understanding of LPS.
However, according to Jun Nakamuro, there are translation errors that should be corrected.
KAIZEN actually means the continuous striving for self-improvement based on the conviction that every person should use his life to live for other people (HANSEI).
Only through the individual aspiration for continuous self-improvement does a change in the physical world in processes, technology or values occur as a result. (KAIRYO)
What we generally understand by KAIZEN is the continuous improvement process (CIP) in the physical world. Employees observe facts at the scene and contribute idea for improvements, which are carefully followed up. However, the CIP is based on the above an attitude and attitude perish.
I think from this detailed breakdown of the KAIZEN concept alone we can see the central role this attitude towards oneself and the employer and the environment plays in the LPS.
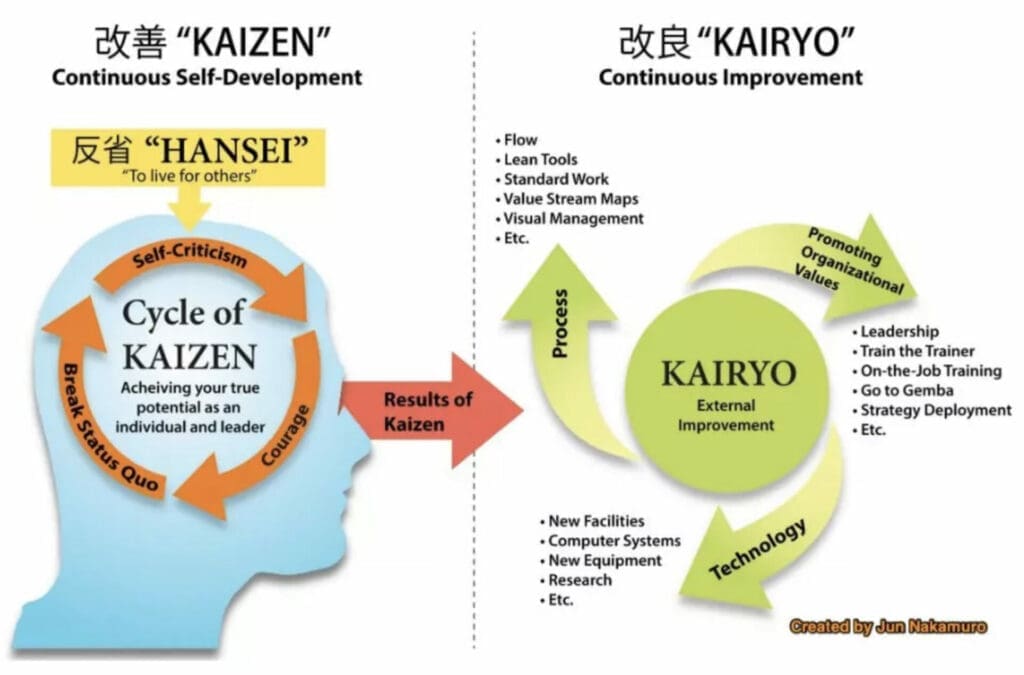
The basis of collaboration
No matter in which industry the LPS is applied, the following tools are always the basis for LPS cooperation.
On the one hand, tidiness and cleanliness in the workplace (“5S/5A” initiatives) lay the foundation for reliability in the first place and establish a culture of appreciation for materials and property.
In addition, a culture of appreciation for employees is established through optimal workplace safety.
The basis for any change is the establishment of and adherence to standards and the delivery of normal performance. “Without standards, there can be no improvement at all.” Taiichi Ohno.
The following applies: Managers who do not manage to establish order and cleanliness, work safety and standards will not be able to establish the more complex tools of the LPS.
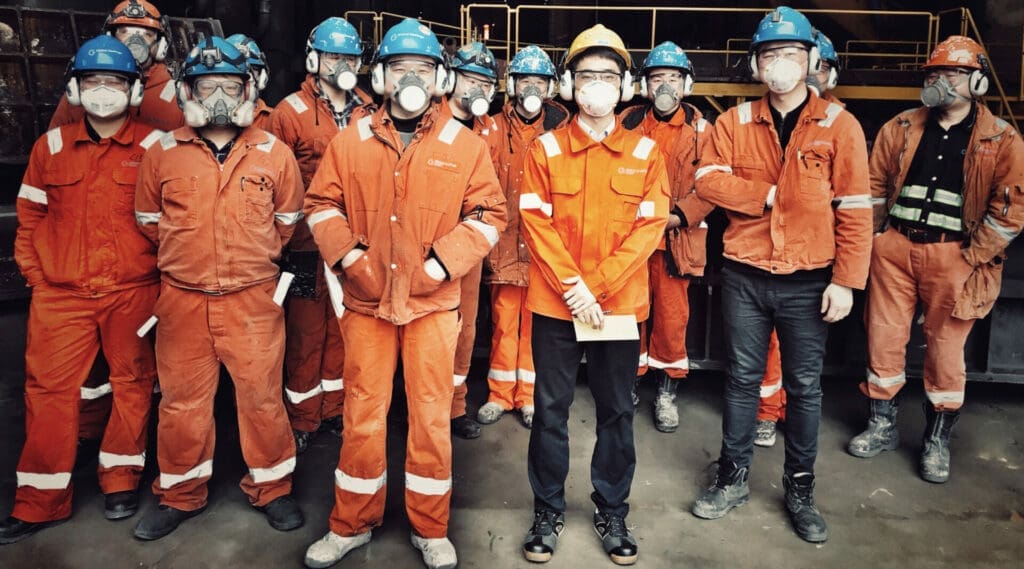
Production sites that show a high standard of order and cleanliness and occupational safety are usually economically successful and also able to implement more complex LPS tools.
Weert Jacobsen Kramer
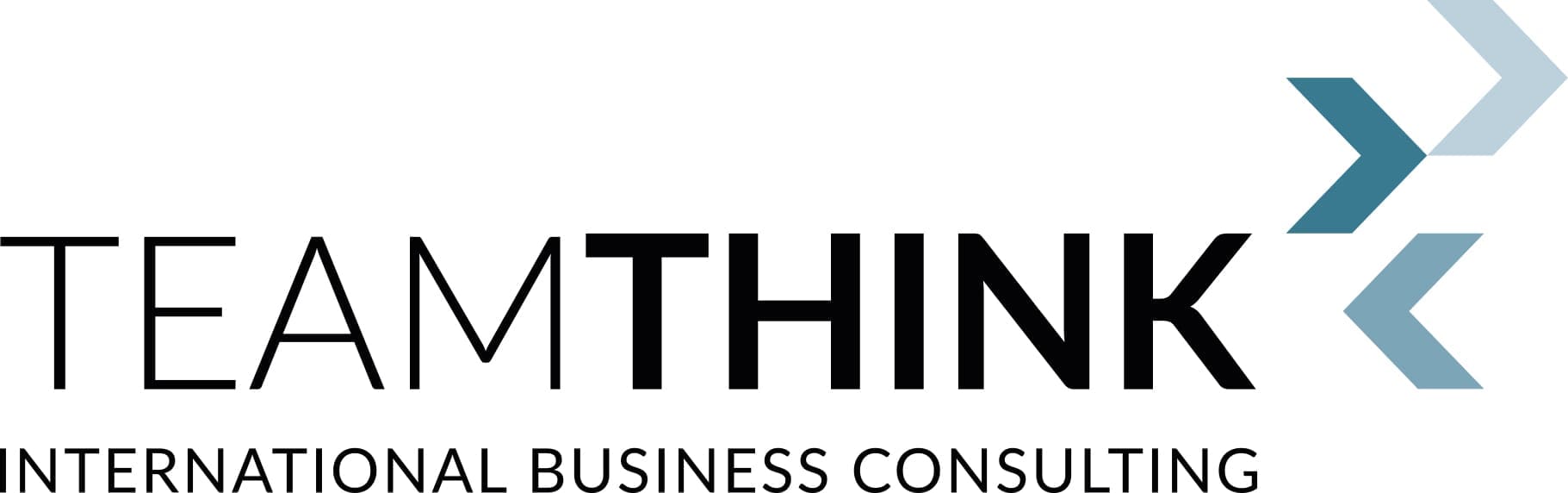
Contact us now!
We have more than 20 years of experience and deliver high quality consulting for your Agile, Lean or Digital Transformation.
Key Performance Indicators (KPIs)
- Durchlaufzeit (Wie lange braucht es vom Rohmaterial bis zum fertigen Produkt?)
- Durchsatz (Wie viele Teile fließen durch den Prozess?)
- Produktivität (Wieviele Output entsteht im Verhältnis zum Input?)
- Liefertreue (Wie Pünktlich wird geliefert?)
- Qualität (Wie hoch ist die Produkt- und Prozessqualität?)
There are five essential KPIs that are usually collected as a baseline before a project and continuously checked for changes.
- Lead time (How long does it take from raw material to finished product?)
- Throughput (How many parts flow through the process?)
- Productivity (How much output is produced in relation to input?)
- Delivery on time (How punctual is the delivery?)
- Quality (How high is the product and process quality?)
Value stream analysis & design & Lean Master plan
How to get a successful start into the Lean Production System (LPS)?
The best way to get started with the Lean Production System is to conduct an analysis of your key value stream. From this analysis, concrete improvement potentials and implementation projects can be derived immediately.
The optimized value stream is defined by a future value stream design. The implementation projects are implemented and controlled by the change team via a central Lean Master Plan.
This way you get to know the Lean way of thinking in practice and immediately reap the benefits of the LPS through concrete improvement of your KPI’s.
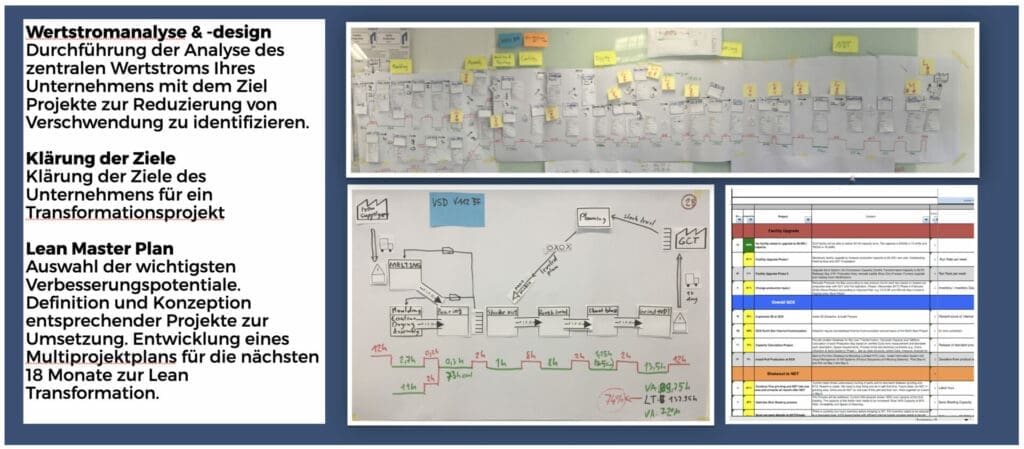
Lean Transformation
Lean is a journey. Once started, this journey never stops. With more and more fascination and enthusiasm you will discover new aspects of the Lean journey and new improvement potentials in yourself, your team, your processes.
Customers often report that they develop a passion for Lean and can no longer imagine a world without LPS. The benefits of LPS are too compelling and pay for themselves, despite all the investment in training and education.
For an initial deep Lean transformation, allow 24 months of project time. You will reach a complete Lean Transformation after about 5 years, depending on the intensity of the efforts.
Start in die Leantransformation
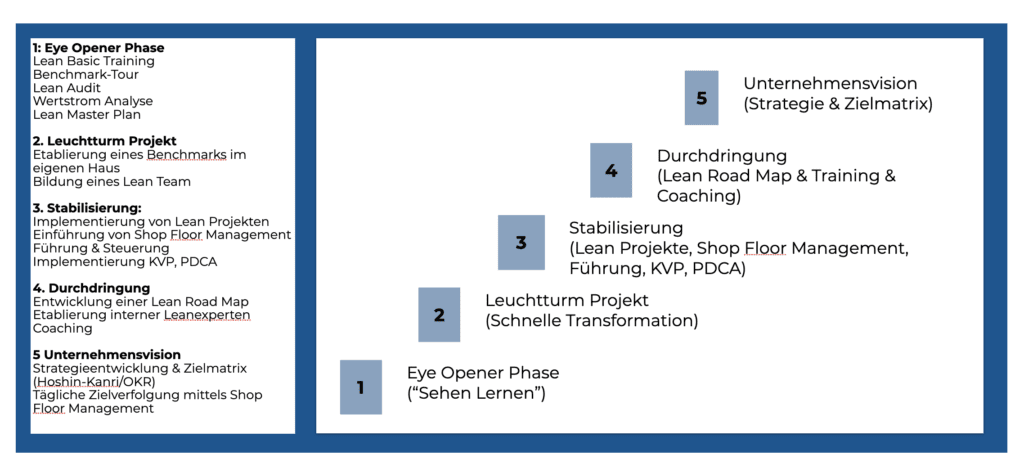
Eye Opener Phase
We conduct a Basic Lean Training and you get to know the LPS first-hand at one of our Best-Practive Partners during a Lean Benchmark Visit. We perform a value stream mapping, define the future value stream design and derive lean projects and a lean master plan.
Lighthouse project
In one area of your company, we establish an internal best practice area that serves as a benchmark example for the rest of the company. An internal Lean team is identified and trained.
Stabilization
The Lean projects are completed step by step. We establish key leadership tools and store floor management for daily operational control. The continuous improvement process (CIP) is developed and initiated and the structured problem solving process (PDCA) is gradually established.
Penetration
Further value stream mapping and the development of a long-term Lean Road Map follow. The internal Lean experts take on more and more responsibility and independently carry out optimization projects.
Company vision
We further develop the strategy of your company, define strategic pillars and target states, as well as concrete goals for the next years. These goals are harmonized across all areas of the company in the X-Matrix.
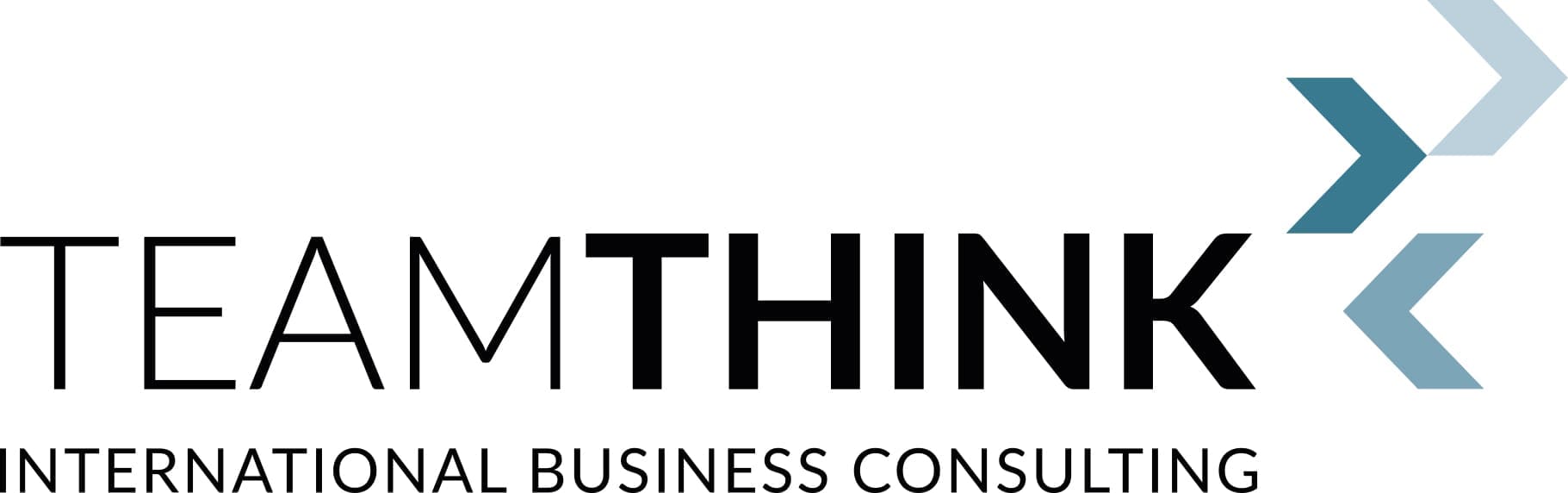
Contact us now!
We have more than 20 years of experience and deliver high quality consulting for your Agile, Lean or Digital Transformation.