Shopfloor Management
Shopfloor Management (SFM) is part of a company’s Performance Management System (PMS) and is a highly effective tool for operational control on the one hand and the exercise of good leadership on the other in the company.
At its core, SFM is about managing deviations from target goals in key value streams of the business: marketing & sales, order fulfillment, and research and development.
The idea of the Shopfloor Management method comes from the Lean Production System (LPS). Here, SFM is used to inform and guide the management of the production teams “at the point of action” (“Gemba”=ShopFloor) on the production floor with the help of well-structured information on team boards within short meetings at the beginning of the shift.
However, the Shopfloor Management method is so successful that this method has also been used for a long time in the “indirect areas” (not directly on the production floor) in the company, e.g. order processing, logistics, development, etc.
Shopfloor Management enables managers to recognize deviations and problem areas at an early stage, to escalate them if necessary, and to initiate structured improvements. These deviations are eliminated directly on site in the team or escalated via the Shopfloor Management cascade. (see below).
The “kaizen mentality” of continuous process improvement and the focus on structured problem-solving are two essential components of the team culture in the context of Shopfloor Management.
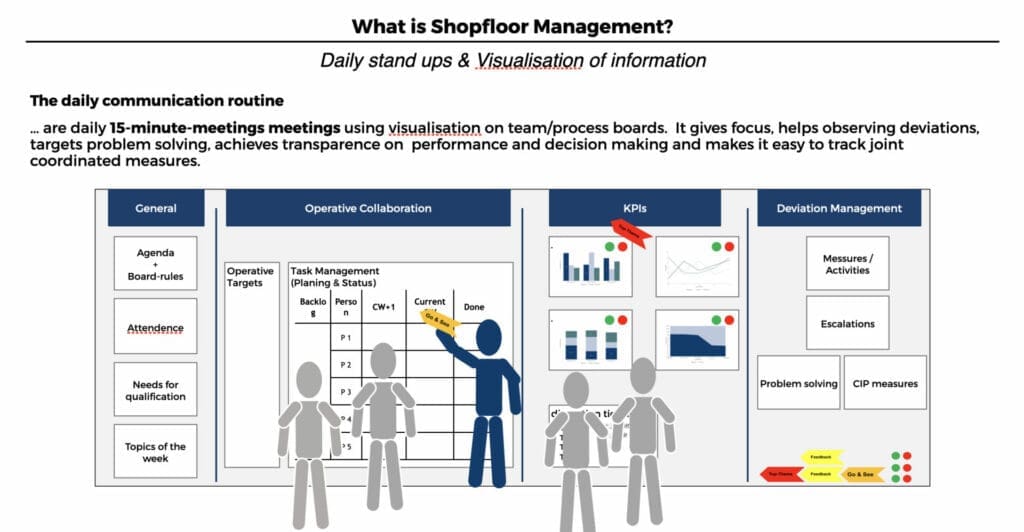
Shopfloor management is less a planning tool, although SFM contributes substantially to the fulfillment of project plans, than a leadership and control tool. The focus is on the operational control of the teams. The focus is on the leadership of the employees.
Daily communication in the context of the Shopfloor Management cascade creates a visualized, structured, channeled flow of information in the company according to fixed rules. The daily meetings are the pulse of the company.
Expert interview: What is shopfloor Management?
- What is shopfloor management (SFM)?
- Is shopfloor management (SFM) effective?
- 2 core elements of shopfloor management (SFM): Visualization and daily stand up meetings
- Shopfloor Management (SFM) is part of the Performance Management
- Board concepts: Task boards vs process boards
- The Shopfloor Management (SFM) Cascade
- The “Performance U” Shape Logic
- Shopfloor Management (SFM) is a leader model
- Digital Shopfloor Management (dSFM) with Valuestreamer
- Culture change and Shopfloor Management (SFM)
Visual Management und Shopfloor Management
The Shopfloor Management method consists of three essential components
- Visual management
“Visual management is the use of visualizations as a management tool and thus an integral part of the lean philosophy. It starts with the idea that problems can only be solved if they are visible – this applies to all areas of the company, from production to administration. The goal of visual management is to inform employees quickly, clearly and efficiently so that each person is able to assess the situation on site at any given time.
Visualization as an information tool for employees is achieved through the use of various coordinated instruments. Audio-visual (graphic, visual and acoustic) instruments of visualization include, for example, information boards, symbols, graphics (A3 report, Ishikawa diagram, Gannt diagram), notices, posters, traffic light indicators and lamps (Andon), maps (Kanban), color markers, acoustic signals and even films. Visualized can be for example:
- produced quantities
- type of goods produced
- key figures
- Group results, both as a guideline for employees and to promote internal competition (absenteeism, productivity, quality, employee qualification)
- Targets and target achievement levels
- Inventories
- Action plans
- implemented ideas
- Work areas (floor markings, internal traffic routes, etc. using uniform colors)
- Workplaces (crack drawings for existing fixtures and tools to mark appropriate storage locations)”
(Quelle: Refa.de)
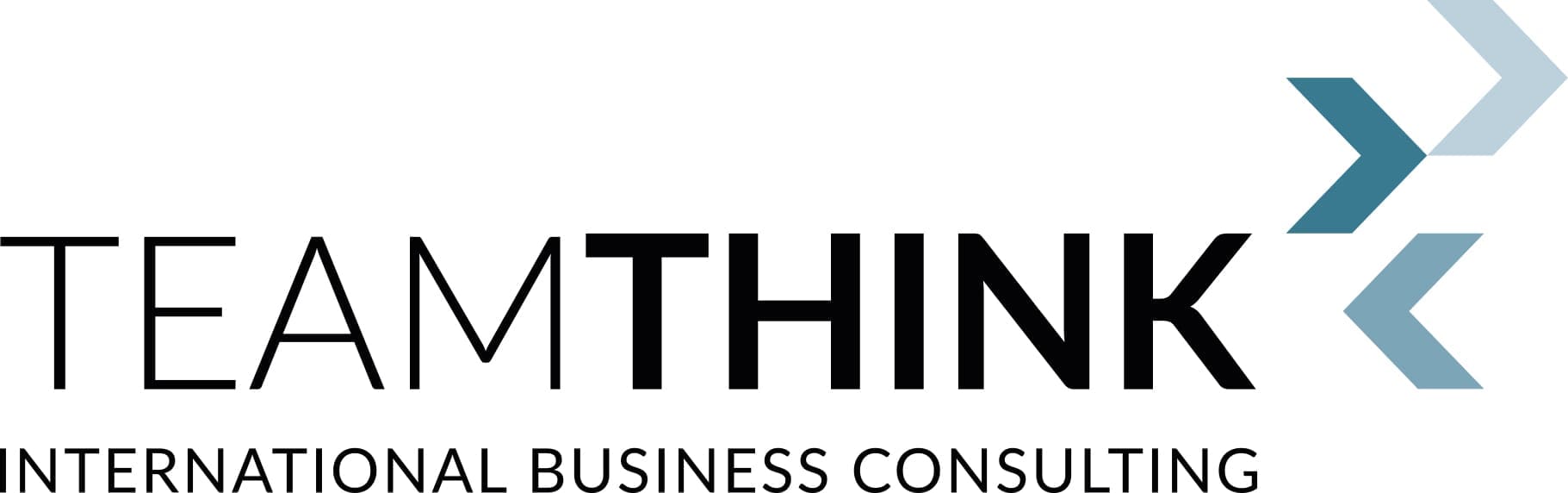
Contact us now!
We have more than 20 years of experience and deliver high quality consulting for your Agile, Lean or Digital Transformation.
2. Team boards or process boards
In the context of store floor management, visual management is used to design the necessary team boards or process boards in a visually optimal way so that information can be easily absorbed and understood by team members.
The design of team boards or process boards is based on five basic considerations, which in turn are reflected on the board.
- Operational control: What information do I need to effectively control operational tasks?
- Measures: What actions do we take to address the variances?
- KPI’s: What metrics do I need to manage the team?
- Problem Solving/KVP: How to enable structured problem solving and continuous process improvement?
- General Information: What other information does the team need?
Team boards
Team boards are used to visualize the tasks to complete specific assignments or projects. The “customer” of the team board is the project team, which uses the board to manage its tasks on a daily basis. The focus is on the distribution of tasks in the team and the delivery of tasks by individual team members or by the entire team.
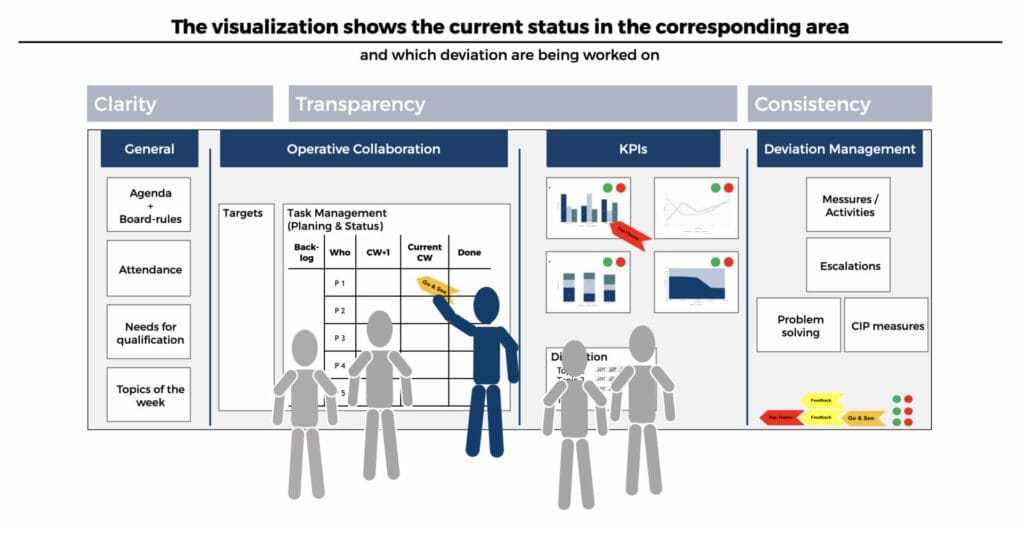
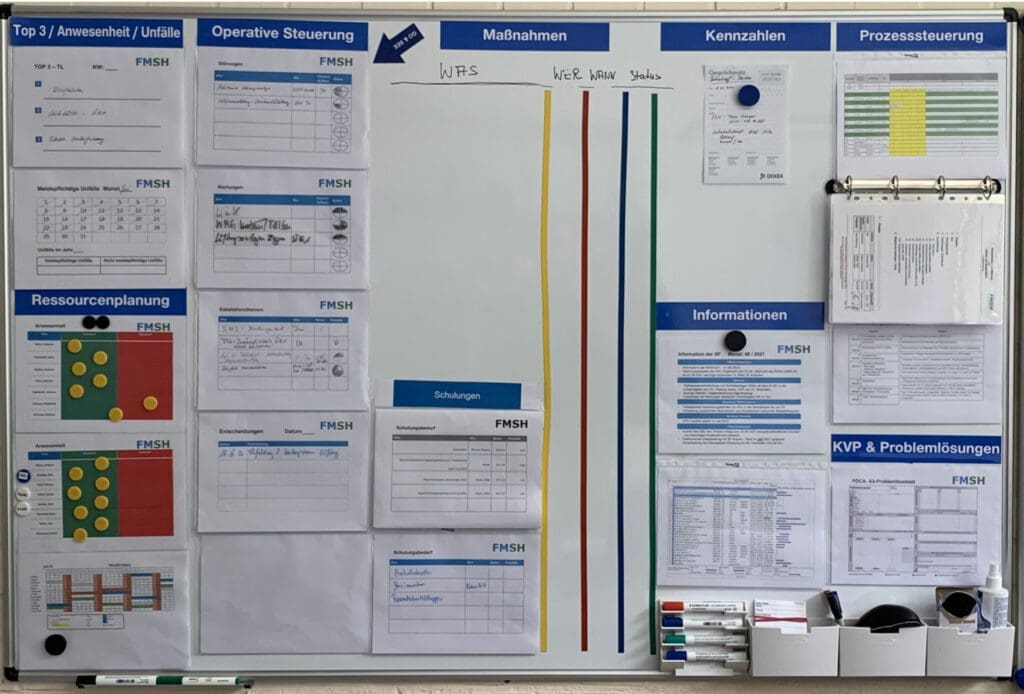
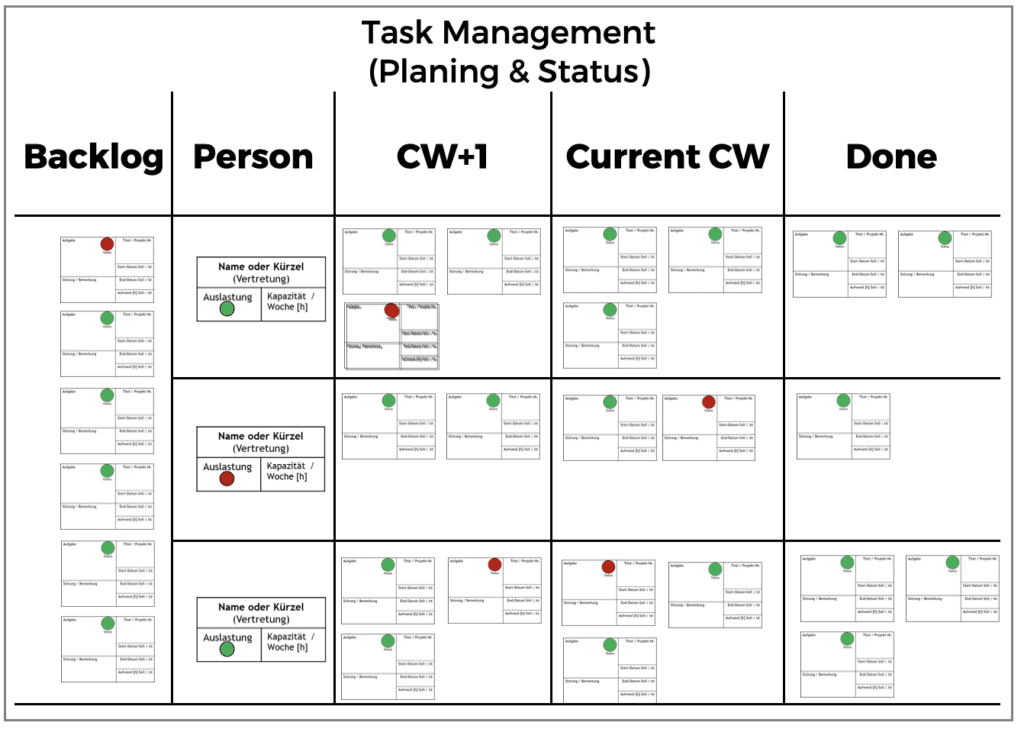
Process boards
Process boards are used to visualize the phases through which a particular process passes in the value stream. Instead of individual task packages, projects are visualized here in the form of project maps. These projects are then moved from one phase to the next depending on the processing status.
The “customer” of the process board is the value stream and thus all the people working in the value stream. Therefore, an interdisciplinary project team or management team usually meets at the process board. The focus is on joint input into the joint project in order to bring this project from one project phase to the next project phase as smoothly as possible.
Work packages are derived from the project status, which are transferred to the respective team boards of the responsible teams and processed there.
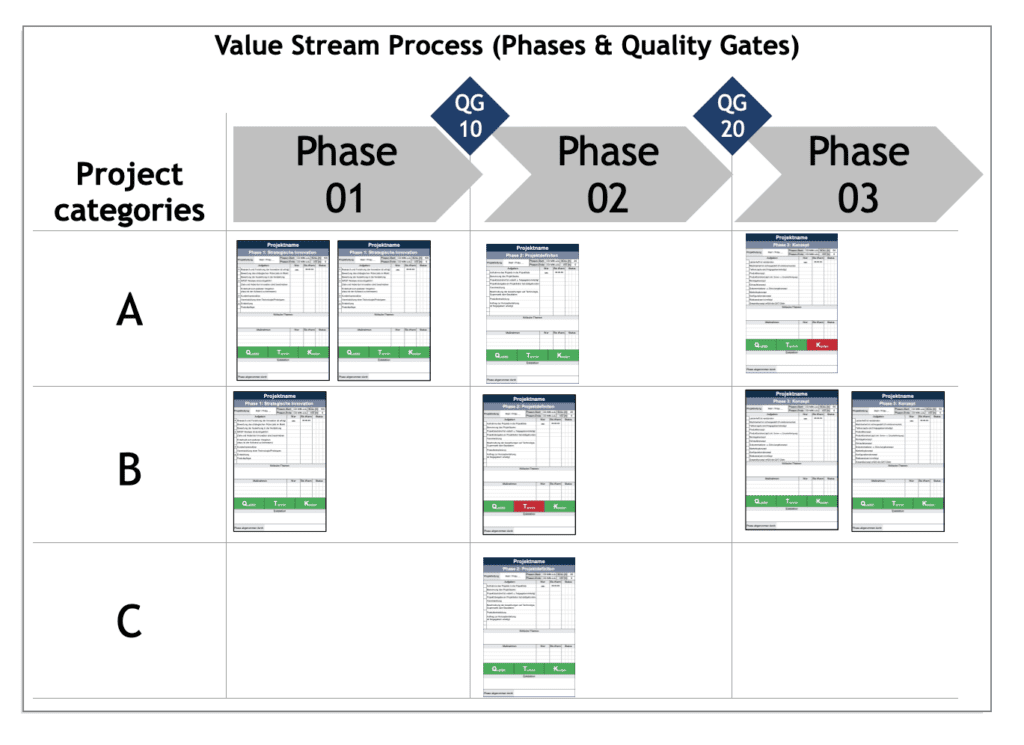

3. Regular communication
The essential core of Shopfloor Management is the daily SFM meetings. The meetings usually last 15 minutes and are held daily across all hierarchy levels at specified times. The meetings are conducted in a standing position and are also called “stand-ups” or “daily’s”.
The daily “stand-ups” are the pulse of the company. Structured, channeled and according to fixed rules, information flows through the entire company.
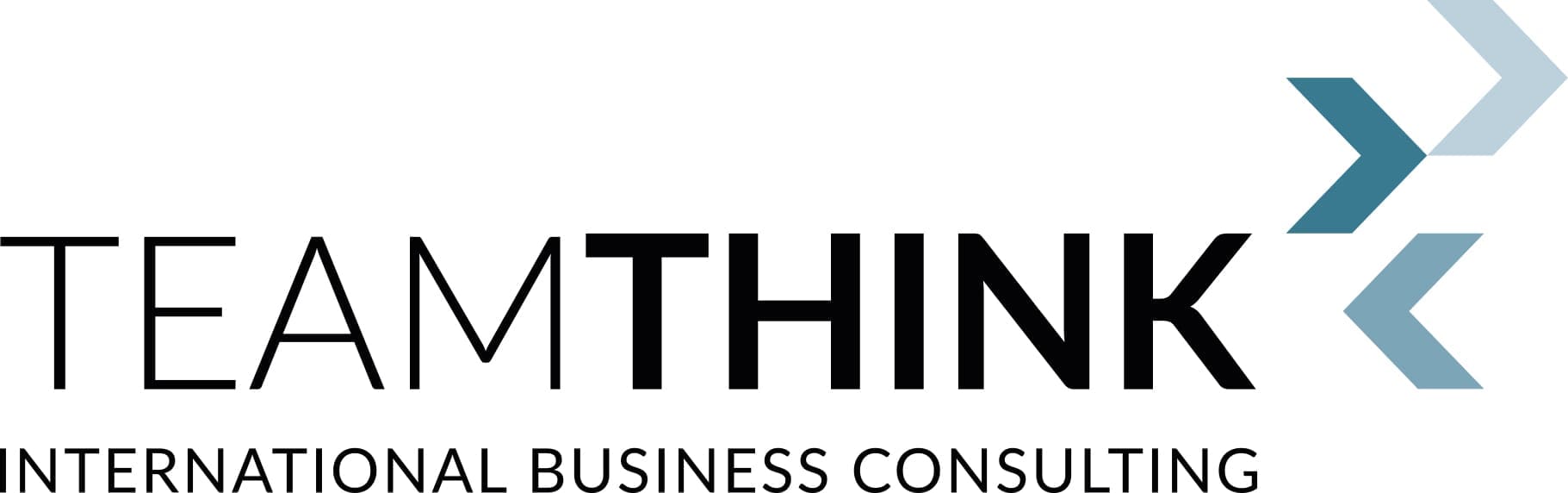
Contact us now!
We have more than 20 years of experience and deliver high quality consulting for your Agile, Lean or Digital Transformation.
Shopfloor Management cascade
Now, the fact is that in a well-established shop floor management cascade, the daily meetings naturally do not take place in just one team.
Rather, the meetings and thus the team boards are usually organized along the line hierarchy. According to the hierarchy, we distinguish between regular communication at team level, at divisional level and at top management level. In terms of time, the meetings of the various hierarchy levels take place in succession.
For example, rule communications at the departmental team level usually take place at 08:30 in the morning. Rule communications at the divisional/departmental level then take place at around 09:30. Rule communications at the top management level usually take place at approximately 11:30 am. The essential element of the Shopfloor Management cascade is the consistent escalation of deviations.
In this way, it is possible for a critical issue to be raised in a team at 08:30 in the morning and to be discussed and decided upon as early as 11:30 in the regular communication of the management/top management. With a decision duration of 3 hours, we are within the target time frame for decision-making in the agile organization.
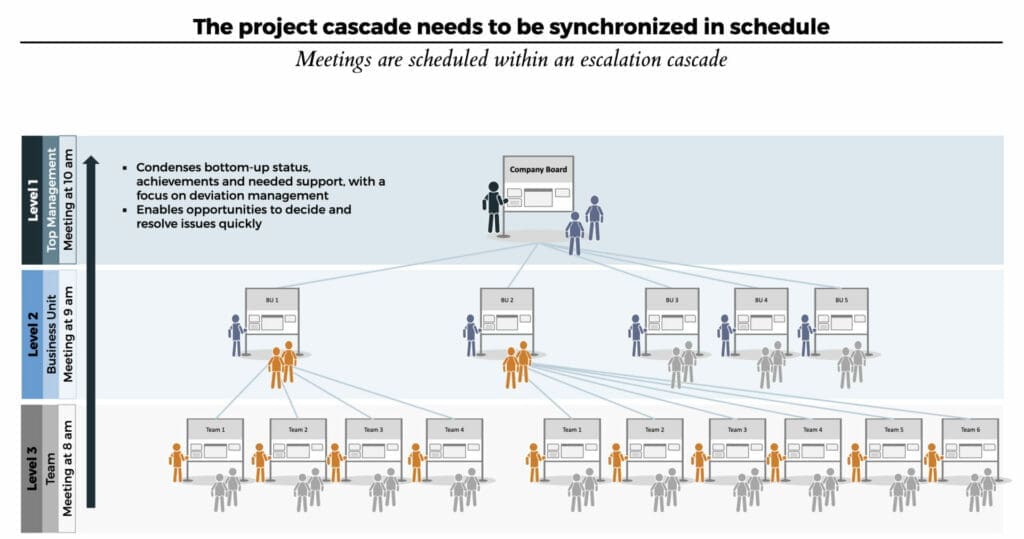
Corporate control center (Obeja)
As part of a complete store floor management cascade, it has become established that companies set up a “corporate control center” for the regular communication of top management. This is a room in the company where all the information from the company’s shop floor management cascade comes together.
Because of the wealth of information that needs to be visualized in the corporate control center, it is an entire room instead of a team board. This room is also called Obeja in Lean Production System.

Multi-project management and performance “U
The store floor management cascade is divided into the process/project cascade and the line/functional cascade according to the performance “U”.
In the process/project cascade, all projects of the company are controlled. This is why this is also referred to as multi-project management. In the project cascade we typically find process boards.
In the line/functional cascade, the task packages for project implementation are controlled. Therefore, we typically find team boards in this cascade.
The planning horizon in project management is based on daily, weekly and bi-weekly deviation management in terms of rolling planning.
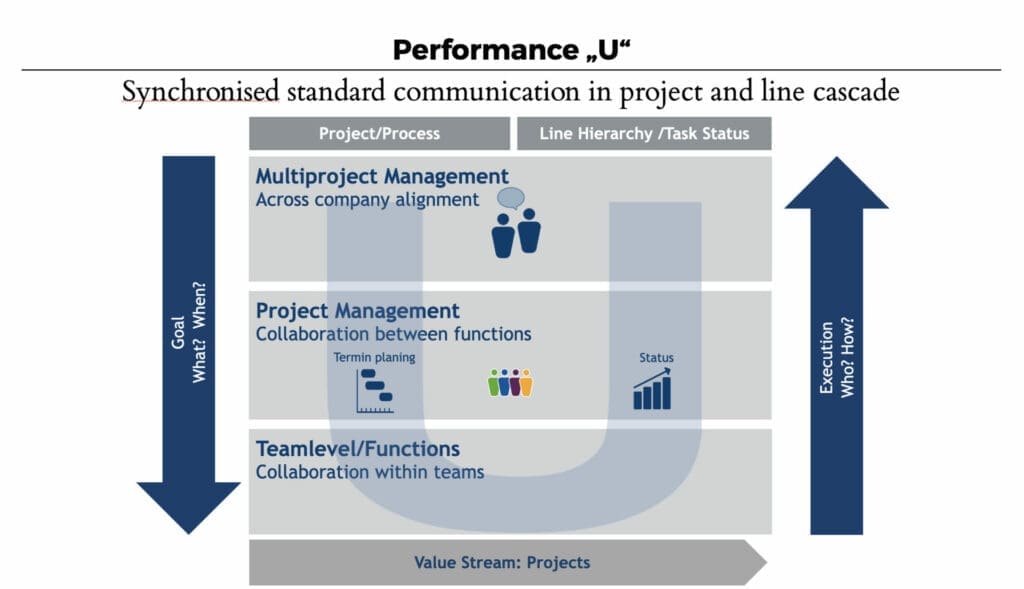
PDCA cycle and CIP process
The shopfloor management cascade is usually ideally supplemented with the PDCA cycle and the CIP process.
The PDCA cycle controls the structured problem solving in the company. Current problems are controlled on the team board within the PDCA cycle and can be prioritized centrally from the top management board so that targeted specific problems are solved in the company.
The CIP process can be controlled from any team board. Important CIP ideas can be escalated via the SFM cascade, or progress or best practice solutions can be communicated to other teams.
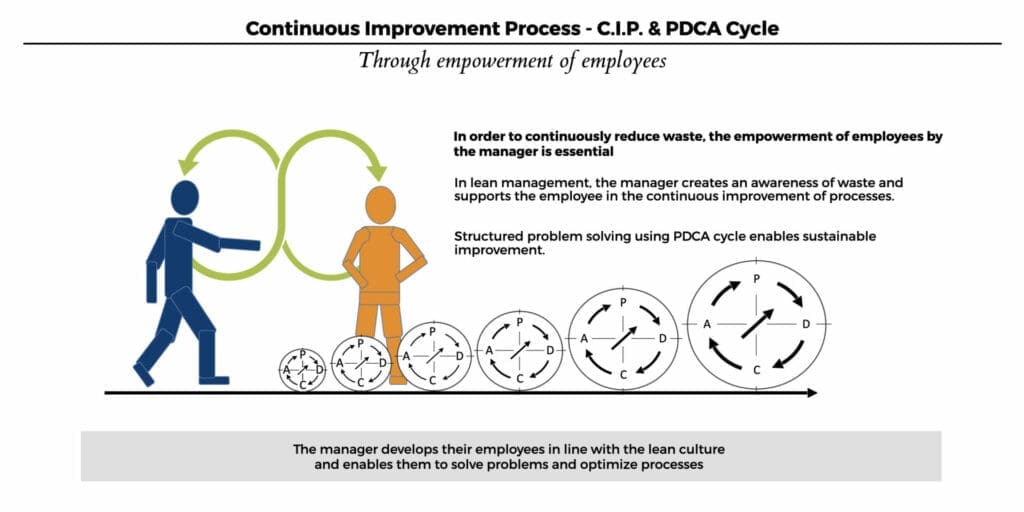
Leadership on the Shopfloor
Shopfloor management (SFM) focuses on specific tasks and requires particular behaviors on the part of the manager and specific management tools.
The executive manages the leadership tasks in Shopfloor Management on site in the team. The manager should take on the roles of disciplinary supervisor, trainer, facilitator and mentor on a situational basis.
In total, there are 6 leadership tasks in the context of Shopfloor Management:
- Conduct regular communication meetings
- Set priorities and make decisions
- Carry out Go& See
- Coach problem solving
- Carry out process confirmation
- Moderate continuous improvement
The behavior of the leader is characterized, among other things, by “leading by asking questions” and “active listening”, as well as by moderating and making decisions.
The SFM tools support the leader in fulfilling his or her leadership tasks. A structured daily routine, standardized rule communications, process confirmation, visualization contribute to the increase of leadership performance.
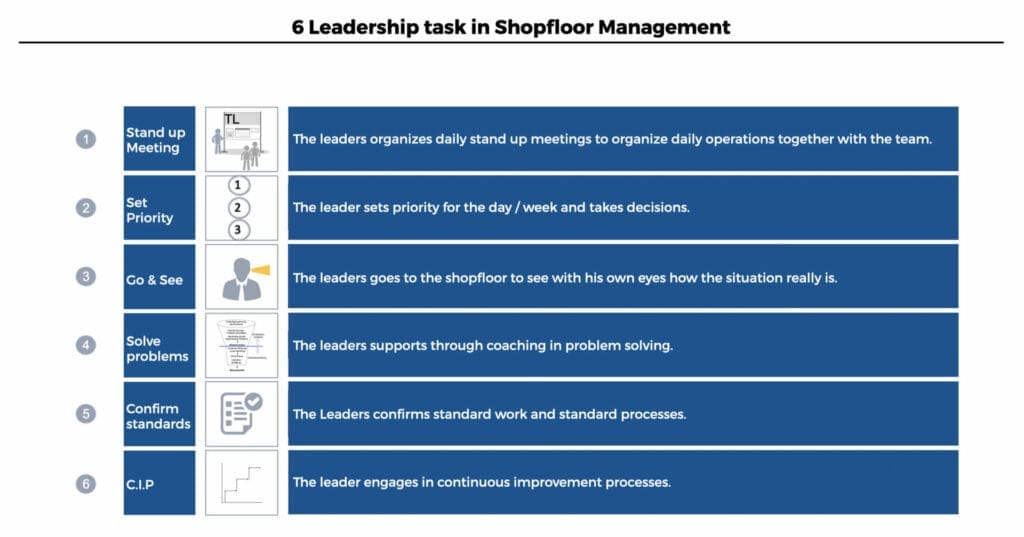
When introducing SFM, the focus is on further developing the professional, methodical and social skills of the executive. This is because the attitude of the manager influences the behaviors and the application of the tools.
It depends decisively on the executive whether SFM is implemented as a tool or contributes to the sustainable top performance of the company by changing the leadership culture.
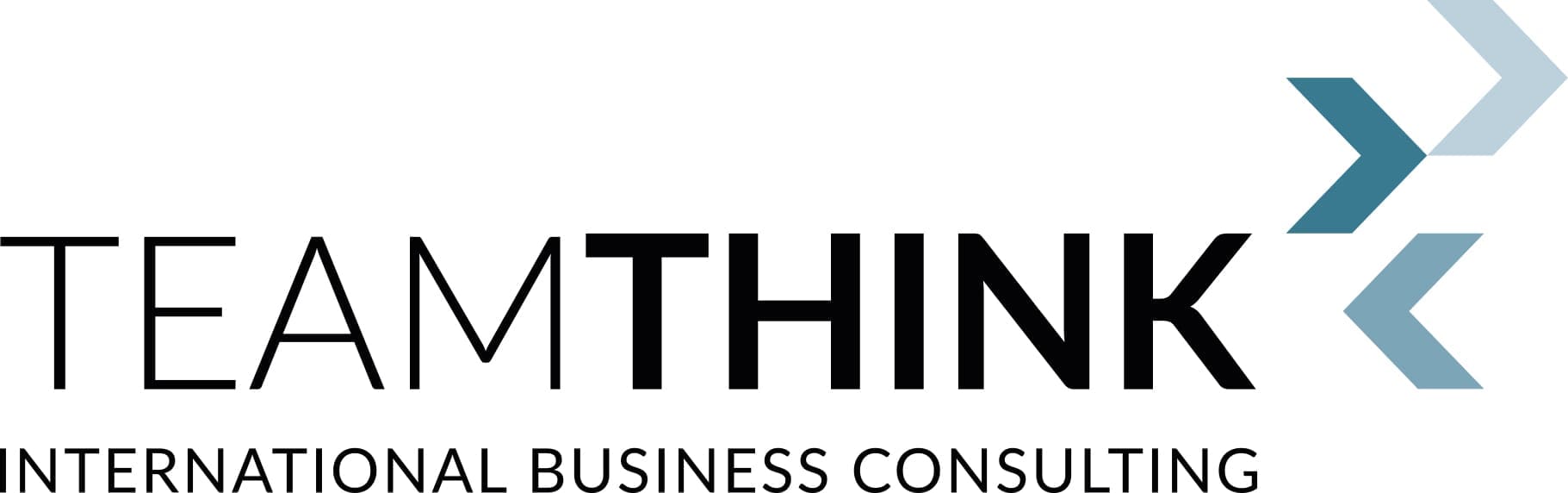
Contact us now!
We have more than 20 years of experience and deliver high quality consulting for your Agile, Lean or Digital Transformation.
Digital shop floor management
Of course, the digitalization of the working world does not stop at the topic of shop floor management. There are now a whole range of software projects and software products that specialize in the implementation of digital shop floor management (dSFM). This results in some advantages and disadvantages, whereby the advantages certainly outweigh the disadvantages:
dSFM Advantages
- Networked control of local units via a global IT system
- Easy creation of cockpits for controlling and managing teams
- KPIs and list elements based on predefined templates to establish global & comparable visualization standards
- Automatic provision of data: KPI, Paretos, etc.
- Real-time data aggregation: Paretos, disruptions, deviations, capacity
- Automated task distribution with linked team boards
- Easy set-up of the store floor management cascade
- Modern digital management instead of “old school” analog store floor team boards
- Management drill-down into activity cascade from rolling wave planning
- Use of dSFM beyond its original function as a control tool as a planning tool
dSFM disadvantages
- Leadership takes place on the computer, human contact is missing
- Development of analog team boards usually takes place together with the team and promotes team development and collaboration culture
- Changes to the board can no longer be made haptically (paper/pencil)
- Comparatively high cost of using the software compared to the low-cost analog paper/pencil solutions.
- The decision for a Shopfloor Management initiative must be coordinated with the IT department and go through budget approval processes.
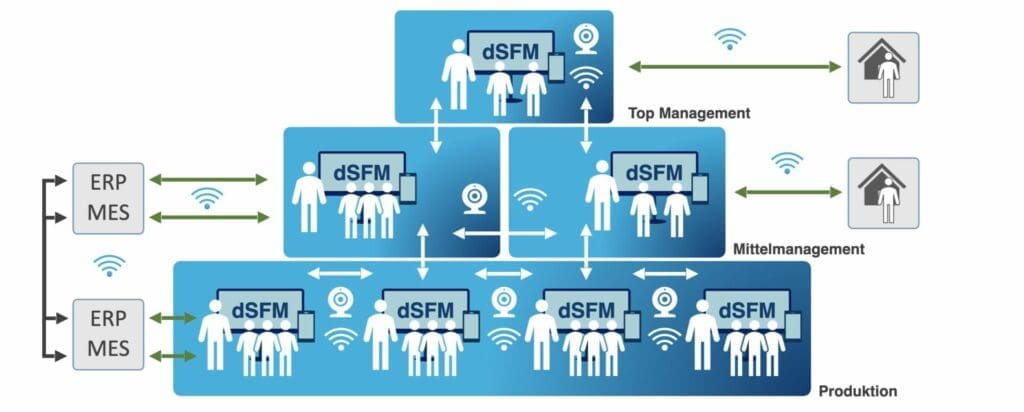
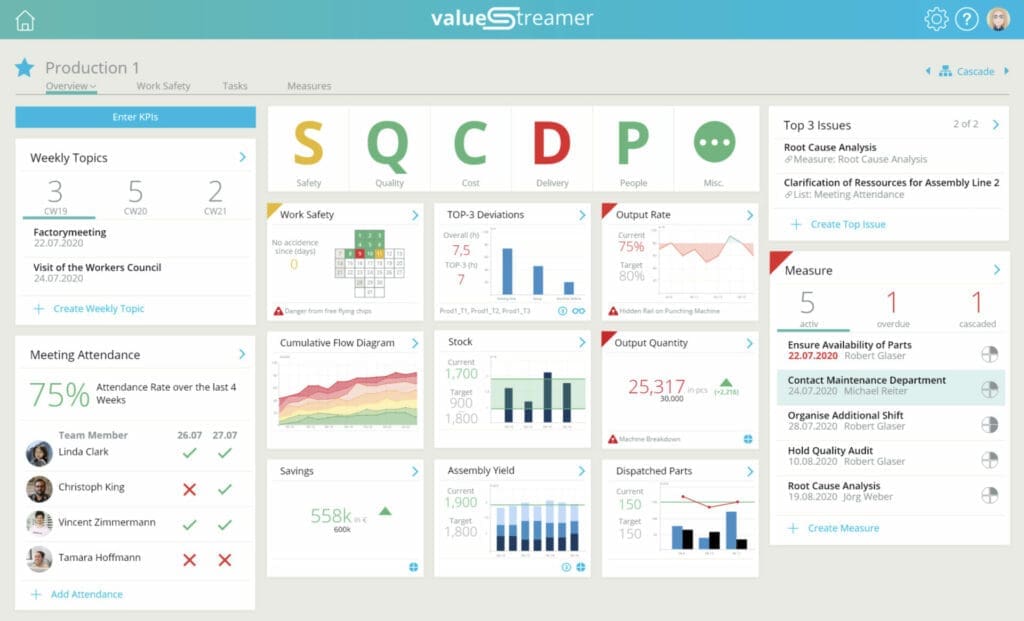
SFM – a prerequisite for the agile organization
The idea of daily meetings in the team, which originally came from the Lean Production System (LPS), as well as short-cycle, iterative coordination with process customers, was taken up by the developers of the Agile project management method.
The visualization of information on “Kanban” boards with the help of “Sticky Notes” have now become an integral part of the Agile work culture.
Many companies are dealing with the mega-trend “Agile Project Management” as well as beyond that with the transformation of the organization from a classic “Hierarchy Organization” into an “Agile Organization”.
The introduction of Shopfloor Management is therefore an important prerequisite for the change to the agile organization.
In the context of structured Shop floor Management, employees learn how to deal with transparent information and how to control deviations in the value stream process through targeted measures. Shop floor management enables effective communication and collaboration within the team and facilitates the transition to an agile organization.
The Agile organization, which is geared towards customer focus, value stream orientation and the processing of work packages in cross-functional teams, in turn needs Shopfloor Management as the method of choice for self-organization in the team for functioning self-management, decentralized decision-making processes and role-based leadership.
So if you are considering developing your organization in the direction of an Agile organization, the first thing you should do is introduce Shop floor Management.
The introduction of store floor management is a culture change project
Of course, cost-intensive consulting projects in industry are launched with the focus on achieving cost reductions through process optimization and productivity increases.
In the context of Shop floor Management, it is important to note that it is a leadership tool that has a significant impact on the corporate culture. The daily transparent task management in the team changes the culture of cooperation because the way of communication changes.
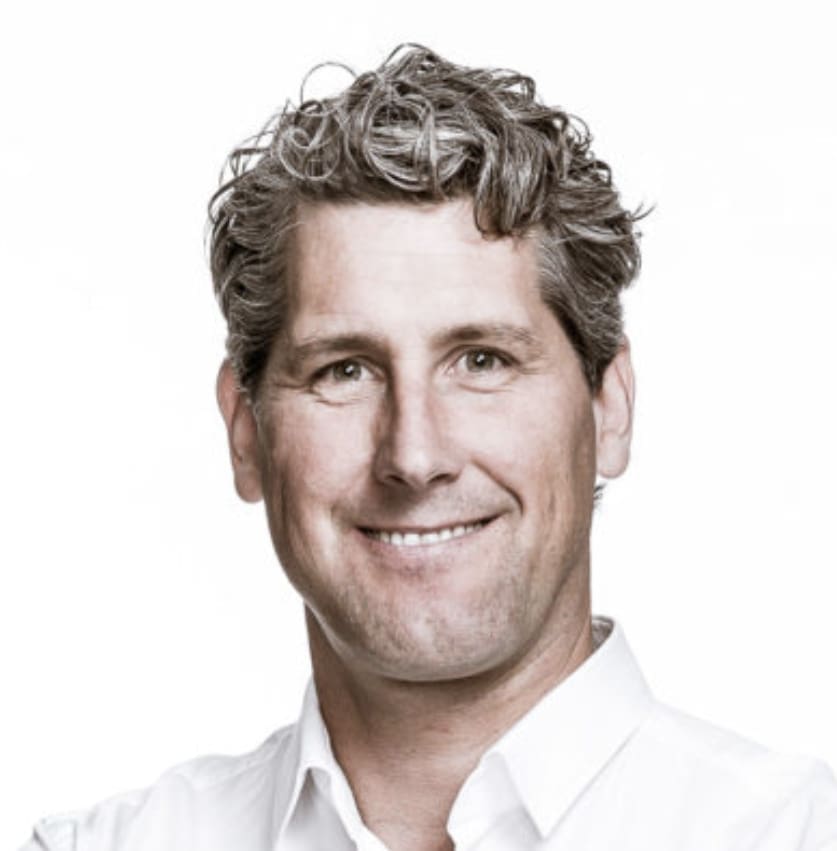
„Social Systems are created through communication. Shop floor management changes communication in the company and is to be understood as a culture change project.”
– Weert Jacobsen Kramer
The corporate culture becomes more open, more forgiving of mistakes and more cordial. The introduction of Shop floor Management changes communication in the company. Companies formerly managed through traditional meetings, PowerPoint presentations and emails are evolving into modern, lean and agile companies where “things move forward”. There is more talking to each other and fewer emails sent to each other for backup. The eternal CC email chains are disappearing, and work results are improving.
Collaboration Exellence
At the heart of the Shopfloor Management method is optimal teamwork. The method is applied by people and at its core it is about enabling successful collaboration within the team.
That is why so much emphasis is placed on the aspects of team leadership and leadership attitude of managers in the application of the Shopfloor Management Method.
It is about good leadership and good collaboration. This leads to the optimal results that the top management of a company wants to achieve.
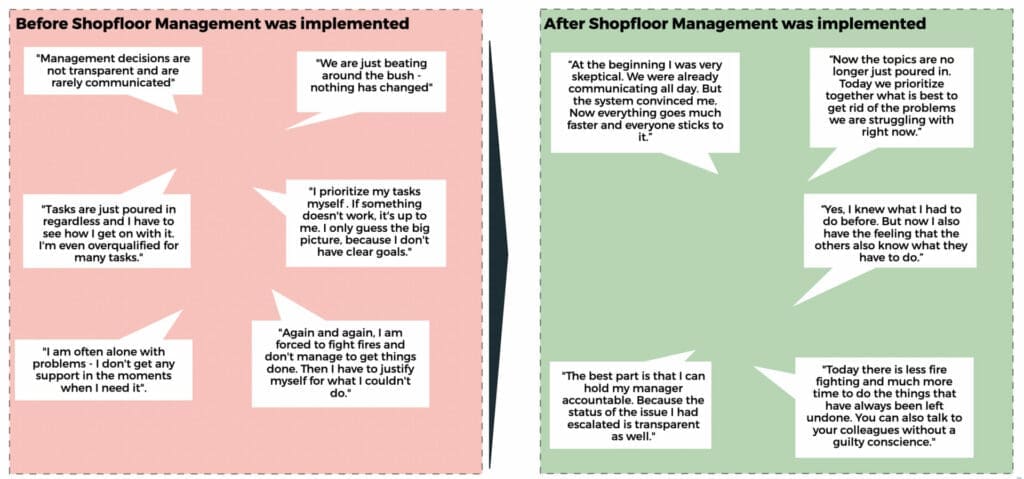
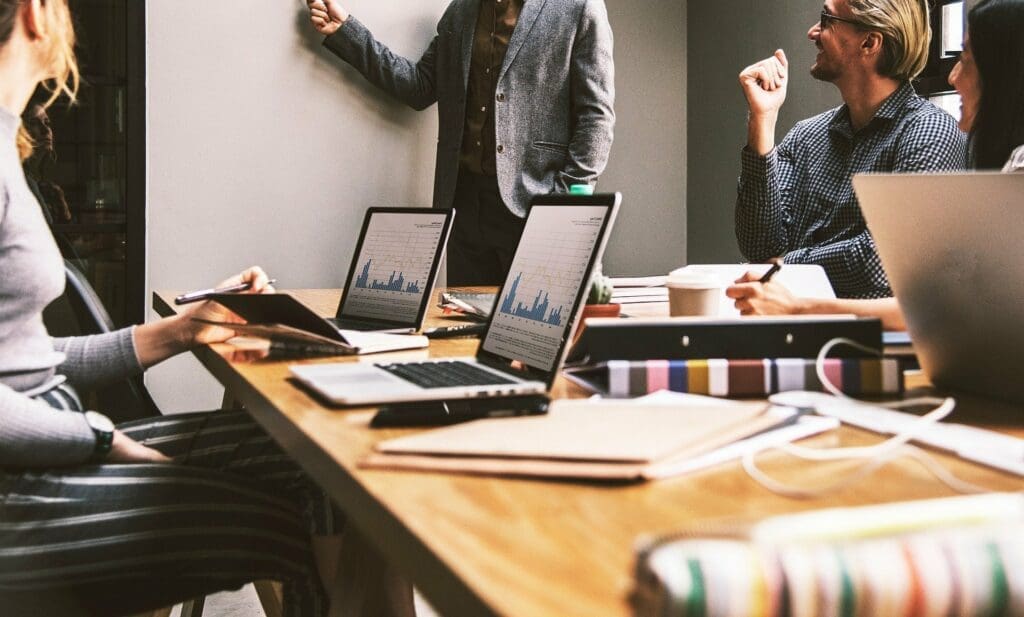
Results
As a rule, it can be observed that the introduction of Shopfloor Management leads to positive changes in the following key figures.
- shorter lead time
- higher adherence to delivery dates
- more throughput
- more transparency in project control
- more efficiency in project control
- more effectiveness in project planning
- more efficiency in communication (less meeting time
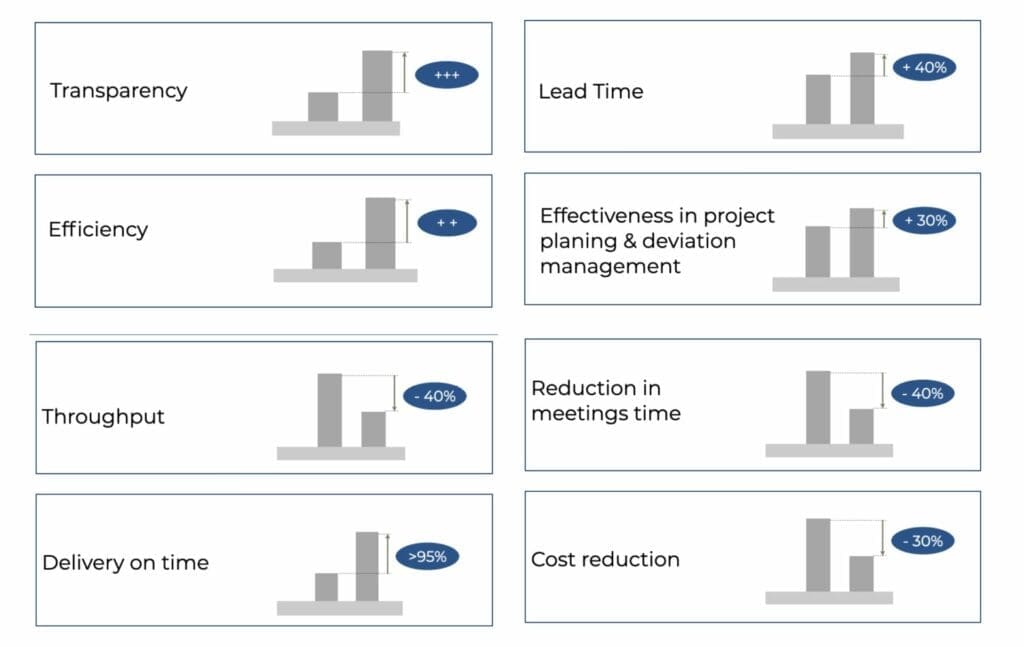
5 phases for the introduction of Shop floor Management
1. Eye Opener Phase
- Lean Basic Training
- Benchmark Tour
- Lean Audit
2. Lighthouse project
- Establishment of a benchmark in the own company
- Formation of a Lean Team
3. Stabilization:
- Shop Floor Management
- Leadership & Control
- Implementation of CIP, PDCA
4. Penetration
- Development of a Lean Road Map
- Establishment of internal Lean experts
- Coaching
5. Corporate vision
- Strategy development & target matrix (Hoshin-Kanri/OKR)
- Daily target tracking by means of store floor management
The introduction of store floor management is a complex change project. You can rely on our many years of experience. We will gladly accompany you. Get in touch with us.
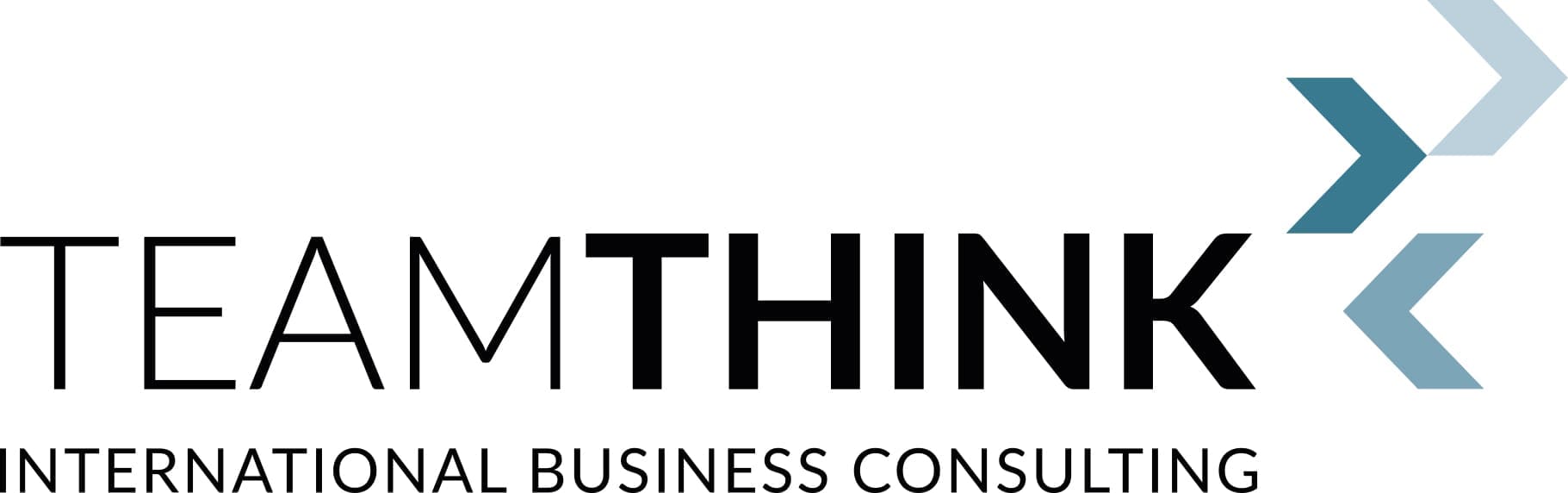
Contact us now!
We have more than 20 years of experience and deliver high quality consulting for your Agile, Lean or Digital Transformation.
HELLO ,
I like more info. about SFM / GK because i work autmotive industry ( parskhodro co.) and implement this system in factory.
thanks a lot.
M.SALIMZADEH
Hello Salimzadeh, please check our Website for more information or contact us. We are happy to assist you on your journey. Kind regards, your TEAMTHINK TEAM
hello,
thanks a lot.
your website is good and usage for me because i worked in automotive industry .
I interest to have your blank formats , is it possible ?
best wishes
M.Salimzadeh